What is the significance of this three-dimensional system? This system offers a novel approach to [insert subject area, e.g., 3D modeling, design, or manufacturing].
This system, encompassing a range of tools and techniques, facilitates intricate designs and complex shapes. It leverages advanced software and hardware to create detailed three-dimensional representations, which can then be used for various purposes, from architectural visualizations to industrial prototyping.
The system's applications are extensive, enabling designers and engineers to visualize concepts in a realistic and interactive manner. This promotes improved design communication and more efficient iteration processes. Furthermore, the three-dimensional approach allows for greater precision and accuracy in manufacturing, reducing errors and material waste. The technology has demonstrably shortened development cycles in various fields.
The subsequent sections delve deeper into the practical applications, advantages, and limitations of this system. Explore how it has transformed industry practices and the potential for its further development.
Jackerman 3D
Understanding Jackerman 3D involves recognizing its multifaceted nature. Its core components and implications are crucial for comprehending its significance.
- Software
- Hardware
- Modeling
- Visualization
- Prototyping
- Applications
- Accuracy
The core elements of Jackerman 3D, encompassing software and hardware, enable complex modeling and visualization. This process, coupled with advanced modeling techniques, leads to highly accurate prototypes. Applications span diverse fields, from architectural design to product development, highlighting the system's versatility. The technology's impact stems from its ability to streamline design processes, reduce errors, and accelerate prototyping cycles in numerous industries, ultimately increasing efficiency and cost-effectiveness. For instance, precision in a mechanical design can lead to a flawless machine operation; architectural visualizations allow clients to truly experience the designed spaces beforehand.
1. Software
Software forms the critical foundation of the Jackerman 3D system. Its functionality dictates the capabilities of the entire system. Sophisticated algorithms and data structures enable the creation, manipulation, and rendering of 3D models. The software's efficiency directly impacts the speed and accuracy of design and prototyping processes. Without robust, compatible software, the potential of the 3D system is significantly diminished.
Specific software components, such as modeling tools and rendering engines, are integral parts of the Jackerman 3D environment. Modeling tools dictate the precision and detail achievable in the 3D models. Rendering engines determine the visual quality and realism of the output, influencing the level of detail and presentation quality. Real-world applications demonstrate this: In architectural design, advanced software allows for highly realistic visualizations of buildings, enabling clients to experience the design before construction. In engineering, precise 3D models facilitate detailed analyses of stress points and optimize designs for functionality and safety. Software thus empowers users with the tools needed to navigate the complex design processes.
A deep understanding of the software's role within the Jackerman 3D system is crucial for optimizing its use. The choice and application of specific software components directly impact outcomes. This understanding allows users to tailor the system's application to specific needs, maximizing the return on investment. Furthermore, awareness of software limitations is essential, as choices of software might restrict the system's design space in some cases. Continuous development and updates of the software components remain paramount for maintaining the system's efficacy.
2. Hardware
Hardware is inextricably linked to the performance and capabilities of the Jackerman 3D system. The specific components and their specifications directly influence the system's speed, accuracy, and overall functionality. Powerful processing units are essential to handle complex calculations involved in 3D modeling and rendering. High-capacity storage is critical for managing large datasets associated with detailed models. Graphics processing units (GPUs) play a crucial role in accelerating rendering times, particularly in complex designs. The interplay between these components determines the system's responsiveness and output quality.
Real-world examples illustrate the importance of hardware. In architectural visualization, high-powered hardware enables the creation of photorealistic renderings, allowing clients to fully comprehend the design before construction begins. In industrial design, rapid prototyping capabilities, facilitated by robust hardware, significantly shorten development cycles. A lack of sufficient computing power can lead to performance bottlenecks, rendering the 3D system ineffective for projects demanding high precision and detail. Conversely, appropriate hardware choices accelerate workflows and improve the quality of the final output.
In summary, hardware constitutes a critical element of Jackerman 3D. Optimizing the hardware configuration is essential for maximizing the system's potential and ensuring smooth operation. Appropriate hardware selections directly affect design processes, project timelines, and cost-effectiveness. The relationship between hardware and software is symbiotic; limitations in one area can hinder the overall efficacy of the system. Understanding these relationships allows users to select hardware appropriate for their specific needs and desired output. The correct hardware choice is essential for project success.
3. Modeling
Modeling within the Jackerman 3D framework is fundamental. It forms the core of the system's capabilities, enabling the creation of digital representations of objects and concepts. This process is crucial for visualization, analysis, and eventual physical realization, significantly impacting design and manufacturing workflows.
- Geometric Modeling Techniques
This facet encompasses various methods for defining shapes and objects. Employing techniques like polygon meshes, NURBS surfaces, or voxel modeling allows for diverse forms and complexities. Real-world applications include architectural designs, where intricate building facades can be accurately modeled, and mechanical engineering, where precise representations of complex machinery are essential. Within the context of Jackerman 3D, these techniques dictate the detail and accuracy of the final model, impacting the quality of subsequent simulations and manufacturing processes.
- Surface Modeling
This aspect focuses on creating smooth and continuous surfaces. It's crucial for applications like product design, where the aesthetics and functionality of a surface are paramount. In the realm of Jackerman 3D, precise surface modeling enables the simulation of lighting, texture, and interactions, ultimately influencing the realism and effectiveness of visualizations. This impacts the user experience in virtual environments and enables more accurate comparisons to the physical product.
- Parameterization and Constraints
This facet involves the use of parameters to define relationships and constraints within a model. This ensures consistency and predictability in design. For example, in industrial design, the ability to adjust dimensions or specifications directly affects the model allows designers to evaluate various configurations rapidly and efficiently. Jackerman 3D's modeling capabilities can streamline design revisions, reduce errors, and increase the speed of prototyping iterations, by applying the correct parameters and constraints in real-time.
- Mesh Generation and Optimization
Converting complex surfaces into simpler, more manageable meshes is vital for rendering and simulation. A key element within Jackerman 3D, mesh generation and optimization significantly impact performance and detail fidelity. This facet enables the trade-offs between visual complexity and processing demands to be effectively navigated, allowing for effective implementation across diverse applications.
In essence, modeling within Jackerman 3D acts as a translator between conceptual ideas and tangible implementations. The techniques, tools, and methods outlined above collectively influence the system's potential and impact on diverse fields. The efficacy of the modeling process directly reflects the system's overall utility and efficiency.
4. Visualization
Visualization within the Jackerman 3D framework is pivotal. It transcends mere aesthetic representation, acting as a critical intermediary between abstract design concepts and tangible products. Effective visualization allows for comprehensive understanding and evaluation of complex 3D models, facilitating improved communication and decision-making throughout the design process. The capacity for realistic rendering and interactive exploration of designs is inherent to the core functionalities of Jackerman 3D.
Real-world examples highlight the significance of visualization. In architectural design, realistic renderings enable clients to experience the proposed building before construction commences, addressing concerns and facilitating approvals. In product design, interactive 3D models facilitate detailed analyses of functionality, ergonomics, and aesthetics, reducing design iterations and improving manufacturing efficiency. These processes highlight how effective visualization significantly accelerates decision-making and streamlines the overall design cycle.
The connection between visualization and Jackerman 3D is causal. Advanced visualization tools are integral to the software architecture of the system. The system's ability to render complex 3D models with high fidelity is directly linked to the quality and efficiency of its internal algorithms and hardware components. This intricate relationship underscores the essential role of visualization in supporting informed decision-making and enabling realistic prototyping processes. Furthermore, the iterative nature of design relies heavily on the insights provided by visualization. The detailed feedback and understanding gained from visualizations directly influence subsequent design stages. Without robust visualization capabilities, the entire design process within Jackerman 3D becomes significantly less effective and efficient.
5. Prototyping
Prototyping is a crucial aspect of the Jackerman 3D system, acting as a bridge between digital design and physical realization. It allows for the creation of tangible representations of digital models, providing valuable feedback for refinement and validation of design choices. The iterative nature of prototyping directly benefits from the system's modeling and visualization capabilities, enabling rapid adjustments and improvements in design. Thorough prototyping within the Jackerman 3D environment minimizes errors and potential issues in subsequent manufacturing stages.
- Rapid Prototyping Capabilities
The system's integration of rapid prototyping technologies allows for the creation of physical models swiftly. This facilitates the testing and evaluation of different design iterations, and identifies any potential design flaws or functionality issues in an early stage. The rapid turnaround time enhances the design refinement process. For instance, in mechanical engineering, rapid prototyping allows for the assessment of stress points and functionality in a tangible model, which are not fully captured through 2D or 2D-based simulations. This is far more effective than relying on computational simulations alone.
- Iterative Design Refinement
Prototyping within the Jackerman 3D environment fosters a cycle of design and refinement. Users can quickly iterate on design elements based on physical testing and user feedback. This iterative process identifies shortcomings and allows for adjustments before extensive manufacturing begins. This iterative approach is invaluable, especially in complex designs where subtle changes can have significant impacts. For example, in architectural design, prototype models allow for the testing of spatial relationships, lighting, and usability before construction. Modifications made during the prototyping stage are instrumental in creating a final product that reflects user needs and expectations more accurately.
- Physical Validation of Design Concepts
Prototyping enables the validation of design concepts in a physical context. This directly addresses the transition from conceptual designs to tangible products. The system allows users to assess the functionality, ergonomics, and overall usability of the design in a practical environment, which offers a more reliable indicator of success compared to theoretical assessments alone. This physical validation is paramount in ensuring the final product effectively meets intended specifications.
- Reduced Manufacturing Errors
By identifying issues in physical prototypes, the system facilitates the mitigation of costly mistakes during mass production. The insights gained from testing prototypes significantly reduce errors in the production phase. For instance, in industrial design, prototype testing reveals potential manufacturing constraints or problematic assembly steps, preventing costly design revisions during later stages. Identifying flaws during prototyping reduces wasted resources and time compared to detecting problems at the manufacturing phase.
In conclusion, prototyping, integrated with the Jackerman 3D system, facilitates a streamlined and efficient design process. The rapid prototyping capabilities, iterative design cycle, and physical validation of concepts contribute directly to achieving better, more functional final products and minimize the chances of costly errors. This integration empowers users with a comprehensive, data-driven approach to design and manufacturing.
6. Applications
The utility of the Jackerman 3D system is inextricably linked to its applications. The system's value proposition is fundamentally defined by its ability to address real-world problems and needs across diverse sectors. Applications serve as the tangible manifestation of the system's underlying capabilities, driving its importance and influencing its development trajectory.
Applications of Jackerman 3D encompass a broad spectrum of industries, leveraging the system's capabilities in distinct ways. In architectural design, the system enables the creation of detailed, interactive models that allow clients to visualize and experience proposed structures. In industrial design, detailed 3D models facilitate the analysis of product ergonomics and functionality, leading to optimized design iterations and reduced production errors. Furthermore, the application in manufacturing extends to precision engineering, enabling the creation of intricate parts and components with enhanced accuracy, minimizing manufacturing flaws. These real-world applications demonstrate the system's practical significance across sectors.
The understanding of applications in relation to Jackerman 3D underscores the system's role as a problem-solving tool. The ability to adapt the system to specific industry needs defines its value. Challenges associated with complex designs and intricate manufacturing processes are effectively addressed by leveraging Jackerman 3D's multifaceted capabilities. Ultimately, the success and efficacy of Jackerman 3D are intrinsically tied to its applicability in various sectors. Future development will likely focus on expanding these application areas, creating new opportunities for innovation and efficiency gains.
7. Accuracy
Accuracy is paramount in the Jackerman 3D system. The precision of 3D models directly impacts subsequent design, analysis, and manufacturing processes. Errors in the initial model propagate through subsequent stages, potentially leading to costly rework or product failures. Maintaining high accuracy is crucial for the system's efficacy and reliability. The fidelity of the digital representation significantly affects the realism of visualizations and the precision of simulations. For example, an architectural model lacking precision in wall thickness or window placement would not accurately reflect the final building. Similarly, in mechanical engineering, discrepancies in component dimensions in a 3D model could lead to assembly issues or compromised structural integrity.
The pursuit of accuracy in Jackerman 3D necessitates a rigorous approach to data input, modeling techniques, and software validation. Careful attention to detail during model creation ensures that the system's outputs accurately represent the intended design. Utilizing advanced modeling tools and techniques minimizes errors inherent in manual processes. Rigorous quality control procedures, including verification and validation checks, contribute to the overall accuracy of the final product. Examples include using laser scanning for precise architectural models, applying advanced algorithms for stress analysis in mechanical design, or incorporating real-world data into the simulations to refine accuracy.
Maintaining accuracy in the Jackerman 3D system is critical for its effective utilization across diverse fields. A system providing accurate models leads to better informed decisions throughout the design cycle. This translates to reduced waste, minimized design iterations, and enhanced product performance. Conversely, a lack of accuracy can lead to costly mistakes, delayed project timelines, and potentially compromised product quality. By prioritizing accuracy at every stage, the Jackerman 3D system can ensure that digital representations reliably translate into tangible, high-quality products, enhancing the value proposition for users.
Jackerman 3D FAQs
This section addresses common questions and concerns regarding the Jackerman 3D system. Clear and concise answers are provided to facilitate a comprehensive understanding of the technology's functionalities, applications, and limitations.
Question 1: What is the core functionality of the Jackerman 3D system?
The Jackerman 3D system encompasses a suite of software and hardware designed for the creation, manipulation, and visualization of three-dimensional models. This includes geometric modeling, surface refinement, and rendering, enabling detailed and realistic representations of objects and designs. The system's core capabilities extend to rapid prototyping, allowing for the creation of physical models from digital representations.
Question 2: What are the key advantages of using the Jackerman 3D system?
Key advantages include improved design communication, accelerated prototyping cycles, enhanced accuracy in design, and a reduction in manufacturing errors. The system's capabilities contribute to cost savings and increased efficiency in various industries, by streamlining the design and development process through detailed visualizations and rapid prototyping.
Question 3: What types of industries can benefit from the Jackerman 3D system?
The system's applications are broad and span diverse sectors. Benefits are realized in industries like architecture, industrial design, manufacturing, engineering, and product development, through its use in tasks such as architectural visualization, product design iterations, and rapid prototyping for manufacturing applications.
Question 4: What hardware components are typically required for the Jackerman 3D system?
Specific hardware requirements vary based on the complexity of the models and the desired level of detail. However, powerful processors, robust graphics cards (GPUs), and high-capacity storage are common components. Adequate RAM and storage capacity are necessary to handle large datasets and complex processes inherent in 3D modeling.
Question 5: What are the limitations of the Jackerman 3D system?
Potential limitations may include software compatibility issues, the need for specialized technical expertise, and the computational resources required for complex models. Additionally, the system's output accuracy is contingent on the precision of input data and the complexity of the models.
In summary, the Jackerman 3D system offers a powerful platform for 3D modeling, visualization, and prototyping. Understanding its core functionalities, applications, and limitations is crucial for optimal utilization and achieving desired outcomes across various industries. Users should consult relevant documentation or technical support for specific guidance on configuration and operation.
The next section will explore specific applications of the Jackerman 3D system in greater detail, illustrating its practical impact across different industries.
Conclusion
The Jackerman 3D system presents a comprehensive approach to 3D modeling, visualization, and prototyping. Key functionalities, including sophisticated software, robust hardware, and precise modeling techniques, contribute to the system's overall efficacy. Applications span diverse industries, highlighting its versatility and potential to streamline complex design and manufacturing processes. The system's ability to produce highly accurate models, coupled with rapid prototyping capabilities, demonstrably shortens development cycles and minimizes errors. Thorough consideration of hardware requirements and software limitations are essential for optimized system performance. The iterative design approach facilitated by the system's visualization and prototyping capabilities ultimately leads to more efficient and cost-effective design implementations.
The Jackerman 3D platform, in its current form, provides a compelling solution for enhancing design processes and accelerating the development cycle across multiple sectors. Ongoing advancements in software and hardware technologies promise further refinements and expansion of its applications. Future iterations of the system should prioritize enhanced user interfaces, intuitive software design, and expanded compatibility with various industry-standard workflows, maximizing the system's value proposition. Careful consideration of future-proofing the technology and anticipating evolving industry demands will be crucial for maintaining its leading edge in the market. A deeper integration with emerging technologies, like augmented and virtual reality, could further expand the system's reach and impact.
- Ryan Reynolds Blake Livelys Stunning Home A Peek Inside
- Ray Romano Everybody Loves Raymond Cast Now Where Are They
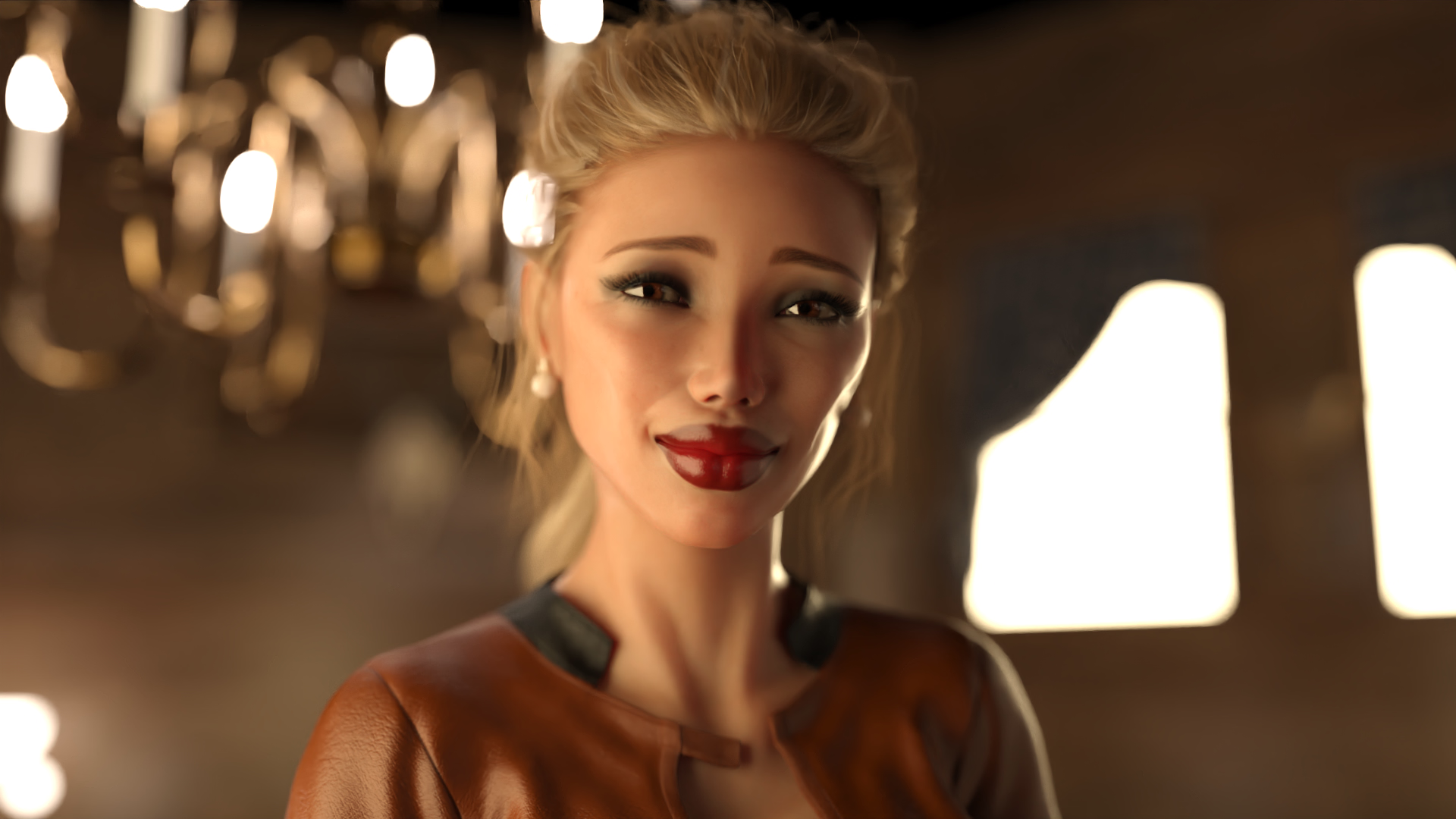
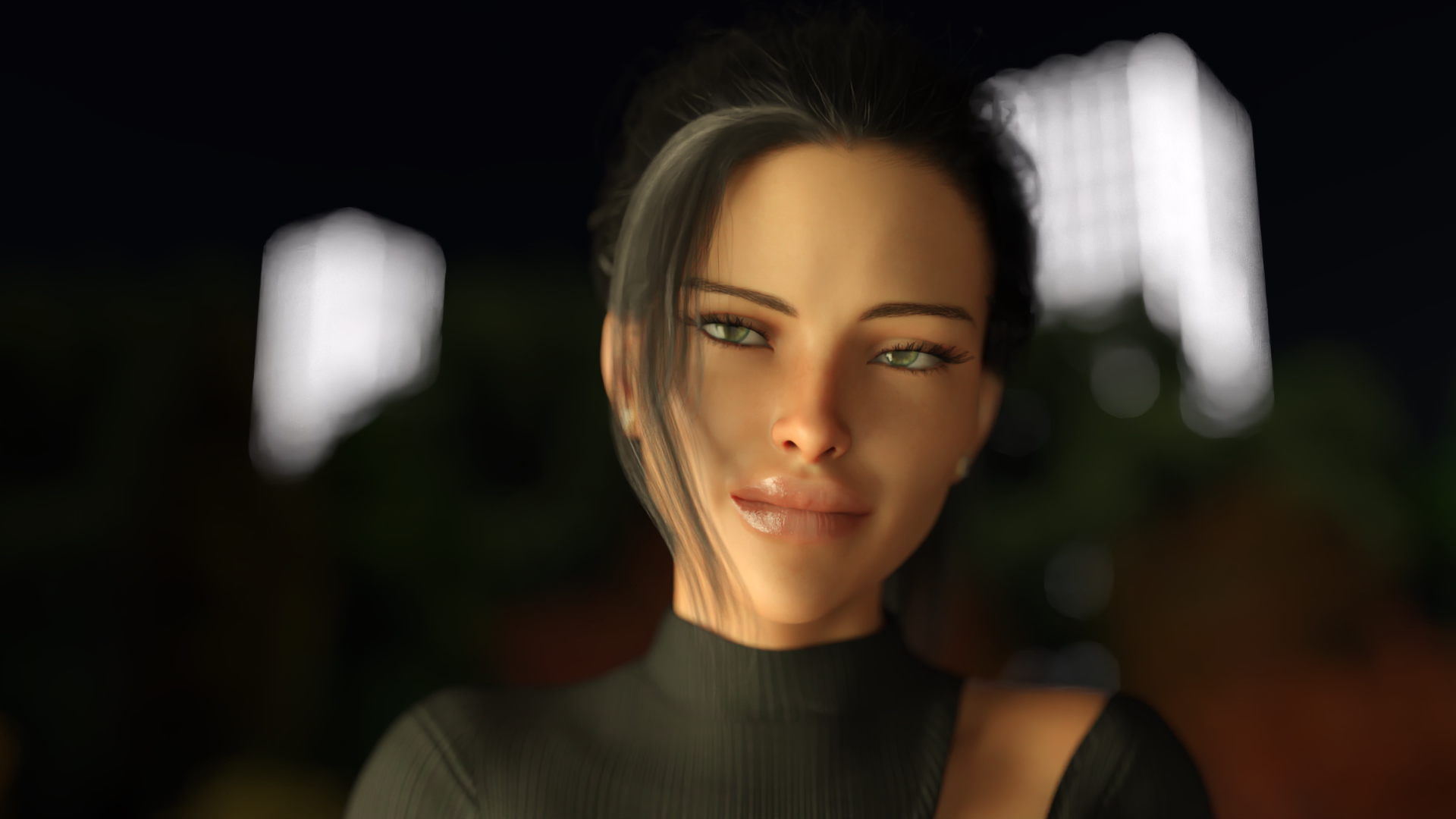
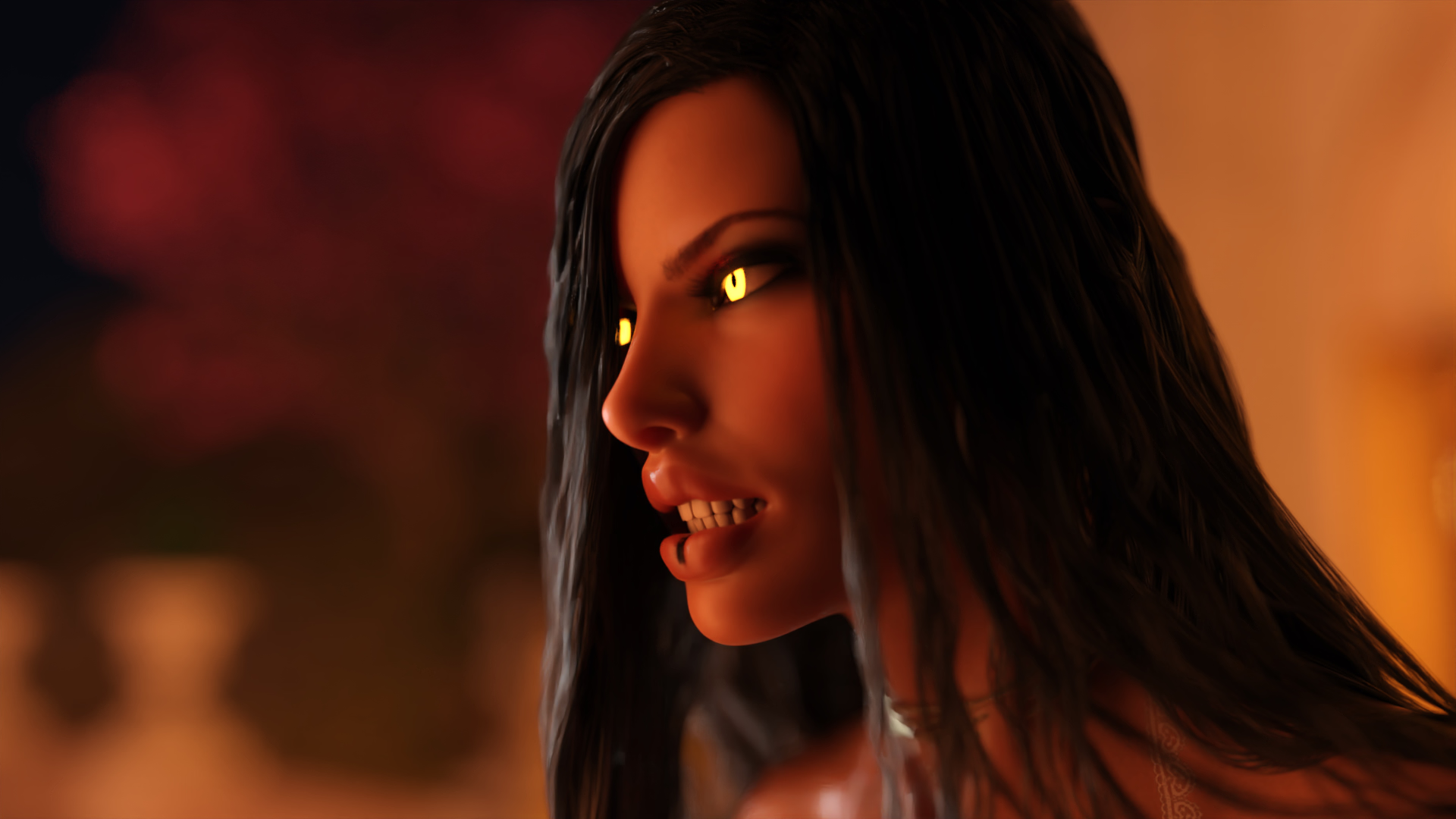