What are the key characteristics of a specific type of rotating machinery and what are its applications?
This rotating machinery component, often utilized in industrial settings, features a unique design for efficient material handling and processing. Its specific configuration allows for a range of functionalities, including precise control and high-throughput operations.
This specialized component plays a crucial role in various industrial processes. Its design facilitates increased productivity by streamlining the flow of materials and enhancing overall operational efficiency. Historical records suggest that improvements in this type of technology have contributed to significant advancements in industrial production, often leading to cost reductions and improved product quality.
Now, let's delve deeper into the specific applications and operational principles of such machinery.
Turner Kufe
Understanding the components and functions of rotating machinery is crucial for industrial processes. This analysis highlights key aspects of a specific type of rotating component, crucial for its functionality and efficiency in industrial applications.
- Design
- Material
- Rotation
- Control
- Support
- Maintenance
- Integration
The design of this rotating machinery component dictates its material selection and ensures suitable rotation speed and control. Efficient support systems are crucial to maintaining accurate operation. Maintenance schedules, carefully planned, minimize downtime. Its smooth integration within larger systems is vital to maximize operational efficiency. A specific type of metallurgy or polymer might be chosen depending on the function and operating environment. Proper maintenance schedules prevent malfunctions, ensuring prolonged operation. Example: A specific design might call for precise lubrication points to enable consistent rotation and minimize wear, contributing to long-term operation with consistent performance metrics.
1. Design
The design of a turner kufe is paramount to its performance. Optimal design considers the material's properties, expected load, and the intended operational environment. A well-designed component ensures consistent performance, minimizes wear, and maximizes longevity. Factors such as the geometry of the rotating parts, bearing selection, and the overall structure play a critical role in determining the efficiency and robustness of the system. Consider a turner kufe in a high-speed application: a poorly designed component might experience excessive vibration, leading to premature failure, while a well-designed kufe would exhibit smooth operation even under demanding conditions. This highlights the direct correlation between design and functionality.
Design considerations extend beyond the immediate component to encompass its integration within a larger system. A suitable design for a turner kufe must consider its compatibility with other machinery components, ensuring smooth material flow and minimal friction. Proper clearance and alignment specifications are critical to avoid potential interference and ensure seamless operation. Real-world examples demonstrate how a well-designed turner kufe can contribute significantly to increased productivity and reduced maintenance costs in various industries. Improved material handling leads to faster throughput and reduced operational bottlenecks.
In conclusion, the design of a turner kufe directly impacts its performance, durability, and integration into broader systems. Careful consideration of material selection, geometry, and operational context is essential to create a highly efficient and reliable component. A deep understanding of design principles allows for the optimization of these components and facilitates their effective integration into industrial processes, ultimately leading to increased productivity and reduced operational expenses.
2. Material
Material selection is critical for a turner kufe's performance and longevity. The material directly impacts the component's strength, wear resistance, and ability to withstand the stresses imposed during operation. Appropriate material choice ensures reliable operation under diverse conditions, such as high temperatures, abrasive environments, or substantial loads. For instance, a turner kufe operating in a high-temperature industrial furnace requires a material resistant to thermal degradation, while one handling abrasive materials necessitates a material with high hardness and wear resistance. Poor material selection can lead to premature failure, necessitating costly replacements and impacting overall system productivity.
The specific properties of the material influence the turner kufe's functionality in several ways. High strength-to-weight ratios allow for lighter components without compromising structural integrity. Materials with excellent thermal conductivity facilitate efficient heat dissipation, minimizing overheating. Corrosion resistance ensures reliable operation in harsh environments, preventing costly component damage and maintenance. The choice of material directly affects the cost-effectiveness of the component. Economical materials with sufficient performance characteristics should be considered. For example, a material with high wear resistance might be chosen for a turner kufe in a mining operation, while a high-strength, low-weight material might be preferable in an aerospace application.
In summary, material selection profoundly affects the performance, durability, and cost-effectiveness of a turner kufe. Choosing the right material ensures the component meets required operational specifications, maximizes its lifespan, and minimizes potential downtime. Understanding the relationship between material properties and the demands of the operational environment is essential for engineers to make informed decisions, ultimately contributing to overall process optimization within the industry.
3. Rotation
Rotation is fundamental to the operation of a turner kufe. The rotational motion of the component is directly linked to its function. A turner kufe's design explicitly leverages rotation to achieve its purpose, whether material handling, processing, or conveyance. The precise speed and regularity of this rotation are critical determinants of efficiency. Variations in rotational speed can significantly affect the throughput rate of the system. Fluctuations in speed can lead to inefficiencies, damage, or even system failure.
Real-world examples demonstrate this principle. In a manufacturing setting, a consistently rotating turner kufe ensures a predictable and reliable flow of materials. This predictability allows for precise timing in subsequent processes, maximizing production efficiency and minimizing waste. Conversely, inconsistencies in rotation can lead to material jams, delays, and quality issues. A turner kufe in a food processing plant, for example, relying on consistent rotation for uniform mixing, demonstrates the crucial link between rotation and consistent product quality. This is critical for maintaining the desired texture and ensuring product homogeneity. Similarly, in industrial machinery involving heavy materials, smooth and consistent rotation of a turner kufe is essential to prevent component strain and ensure longevity.
Understanding the interplay between rotation and a turner kufe is essential for optimal system performance. Engineers must carefully consider the rotational dynamics, including torque, inertia, and frictional forces, when designing and operating these components. Failure to account for these factors can lead to malfunctions, reduced efficiency, and potentially catastrophic failures. Accurate calculation of rotational forces and precise speed control are indispensable for maintaining consistent quality and throughput in applications involving turner kufes. A solid understanding of rotational mechanics, in the context of a turner kufe, allows for the optimization of industrial processes, reducing downtime and maximizing efficiency.
4. Control
Precise control is intrinsic to the functionality of a turner kufe. The ability to regulate the component's rotational speed, direction, and torque is paramount. Without effective control mechanisms, the kufe's operation becomes erratic, leading to material handling issues, potential damage to the system, and decreased overall efficiency. Control systems are therefore crucial for maintaining consistency and preventing errors in the process.
Control mechanisms in a turner kufe manifest in various forms, from simple on/off switches to complex feedback loops. Sophisticated control systems, often employing sensors and programmable logic controllers (PLCs), enable dynamic adjustments to rotational speed and direction in response to changes in material properties or operational demands. Real-world examples abound: in a manufacturing process handling diverse materials, precise control of the turner kufe's rotation allows for the appropriate handling of each type. An automated system with varying speeds for delicate components or heavier materials is vital for consistent quality and prevents damage. Furthermore, in applications where materials are sensitive to temperature fluctuations, regulated speed control, monitored via feedback systems, is crucial for preventing overheating and potential quality defects.
Effective control of a turner kufe is not merely a technical necessity but a key factor in optimizing industrial processes. Precise control minimizes downtime, improves product quality, and enhances overall productivity. Maintaining consistent and predictable rotational patterns within the turner kufe is crucial to avoid material damage, ensure accuracy, and improve throughput. Failure to implement robust control systems can result in significant operational challenges and costly production setbacks. Ultimately, a comprehensive understanding of control systems and their integration within the turner kufe is essential for maximizing output and minimizing potential operational risks in various industrial settings.
5. Support
The effective operation of a turner kufe hinges critically on the support systems in place. Adequate support structures are not merely supplementary but integral components, directly impacting the kufe's ability to perform its function reliably and efficiently. Robust support systems are essential for withstanding the forces and stresses inherent in its operation, ensuring stability and minimizing vibrations, thereby preventing potential damage. Insufficient or poorly designed support can lead to premature failure, necessitating costly replacements and disruptions to production.
Consider a turner kufe in a high-speed application. The rotational forces generated at these speeds are substantial, and without appropriate support bearings and mounting structures, the component is prone to misalignment, vibrations, and ultimately, failure. Similarly, in applications involving heavy materials, the support structure must bear significant loads. Inadequate support can compromise the integrity of the component and the overall system, potentially causing material damage or even safety hazards. Real-world examples highlight the critical role of support structures in preventing operational interruptions and ensuring consistent performance in these contexts. Careful consideration of support systems during the design phase is, therefore, crucial to mitigate risk and enhance the longevity and reliability of the turner kufe.
In essence, support systems for a turner kufe are not secondary elements but crucial components defining the kufe's operational integrity. Appropriate design and implementation are vital for sustained performance, minimized downtime, and overall system efficiency. A thorough understanding of the forces acting on the kufe and the chosen support mechanisms is critical to predict, mitigate, and prevent potential failures. This understanding directly translates to improved safety protocols, enhanced productivity, and reduced maintenance costs in industrial environments. The absence of adequate support will significantly impact the reliable functioning of the turner kufe and the processes it facilitates.
6. Maintenance
Regular maintenance is essential for the reliable and efficient operation of a turner kufe. Proactive maintenance procedures safeguard the component's integrity, prevent unexpected failures, and minimize downtime, which are critical in maintaining production output. Neglecting maintenance can lead to costly repairs, decreased lifespan, and safety hazards.
- Preventive Maintenance Schedules
Establishing and adhering to a preventive maintenance schedule is crucial. This involves routine inspections, lubrication, and cleaning to identify potential issues before they escalate into major failures. Regular lubrication, for instance, minimizes friction and wear, ensuring consistent rotational speed and preventing overheating. Visual inspections for signs of damage, such as cracks or misalignment, are vital for early detection and timely intervention. Scheduled replacement of components, like bearings, based on predetermined cycles or operational hours, can further enhance the reliability and reduce the risk of breakdowns. An example would be a scheduled lubrication and inspection every 100 operating hours.
- Predictive Maintenance Techniques
Advanced predictive maintenance techniques, incorporating sensors and data analysis, can anticipate potential failures. Monitoring vibration levels, temperature fluctuations, and other operational parameters allows for proactive interventions. For instance, if sensors detect unusual vibrations exceeding predetermined thresholds, it signals the need for immediate investigation and potential repairs. Real-time data analysis can predict when components, like bearings, are approaching their service life and help in optimizing replacement strategies, reducing unplanned downtime. Data analysis can identify patterns indicative of wear and tear, enabling better forecasting of required maintenance.
- Corrective Maintenance Procedures
Implementing effective corrective maintenance procedures is necessary when failures occur. Prompt identification and repair of issues minimize the impact on production and prevent further damage. This includes timely replacement of damaged components, adjustments to operational parameters, and addressing underlying causes to avoid recurring failures. A systematic approach to documenting failures and their causes is vital for learning from past incidents and improving future maintenance strategies. A corrective maintenance protocol would include a detailed procedure for replacing a bearing and addressing lubrication issues post-failure.
- Personnel Training and Expertise
Proper training for personnel responsible for maintenance is essential. Adequate training equips technicians with the necessary knowledge and skills to identify and address issues correctly. This includes training on safety procedures, diagnostics, repair techniques, and utilizing specialized tools and equipment. Qualified personnel are crucial for maintaining the complex systems that a turner kufe is part of. Training programs should include safety procedures specific to the type of machinery involved, to prevent accidents and incidents.
Effective maintenance strategies, encompassing preventive, predictive, and corrective measures, are crucial for optimizing the performance and lifespan of a turner kufe. By prioritizing maintenance, industrial facilities can minimize unexpected downtime, ensure consistent output, and mitigate safety risks. Regular maintenance not only reduces costs associated with unforeseen repairs but also prevents significant production losses and the potential for accidents.
7. Integration
The successful implementation of a turner kufe within a broader industrial system relies heavily on its seamless integration. This encompasses the component's compatibility with other machinery, its impact on overall workflow, and the consideration of factors like space limitations and power requirements. Effective integration minimizes operational disruptions and maximizes efficiency within the manufacturing or processing process.
- Mechanical Compatibility
A critical aspect of integration involves ensuring the turner kufe's mechanical compatibility with existing machinery. This necessitates careful consideration of dimensions, mounting points, and interfaces. Misalignment or incompatibility can lead to operational inefficiencies, increased wear on components, and potential equipment damage. Precise measurements, detailed schematics, and rigorous testing during the integration phase are crucial to avoid these issues. For example, a poorly integrated turner kufe might result in material jams or excessive friction due to incompatible shaft sizes, impacting overall productivity.
- Power and Control Integration
The turner kufe's integration demands careful planning of power supply and control systems. Compatibility of voltage, amperage, and control signals is essential for reliable operation. Interfacing with existing control systems, ensuring proper feedback mechanisms, and integrating safety protocols are critical to prevent malfunctions or operational hazards. For instance, an inadequate power supply could lead to insufficient torque, affecting the kufe's ability to handle materials efficiently. Similarly, a lack of integration with safety systems could introduce risks to personnel and the machinery itself.
- Workflow Optimization
Integration goes beyond mechanical and electrical compatibility; it also entails optimizing the workflow. The turner kufe should be positioned within the production line to maximize material flow and minimize bottlenecks. Careful analysis of the existing production process, including material handling stages, should inform the optimal placement and configuration of the turner kufe. For example, strategic placement of the kufe can minimize transport distances, reduce handling time, and improve overall throughput. Conversely, poor integration could create delays and inefficient material flow.
- Environmental Considerations
Environmental factors, such as space constraints, temperature fluctuations, and noise levels, must be considered during integration. The turner kufe's design and placement must accommodate the existing space and operating conditions. Solutions for noise mitigation and dust control must be factored in. Poor consideration of these factors can lead to operational difficulties, decreased efficiency, and negative impacts on the working environment. For instance, inadequate noise control mechanisms could result in worker discomfort and reduced productivity. Poor placement with respect to environmental conditions could lead to corrosion, affecting the component's durability.
In conclusion, the successful integration of a turner kufe is a multifaceted process encompassing mechanical compatibility, power and control integration, workflow optimization, and environmental considerations. Thorough planning, careful design, and rigorous testing are vital to ensure the kufe operates seamlessly within the existing system, contributing to enhanced productivity, efficiency, and safety. Failure to address these aspects can significantly compromise the benefits expected from the implementation of a turner kufe.
Frequently Asked Questions (Turner Kufe)
This section addresses common inquiries regarding turner kufes, providing concise and informative answers to facilitate understanding of this rotating machinery component.
Question 1: What is a turner kufe, and what is its primary function?
A turner kufe is a specialized rotating component used in industrial machinery. Its primary function is material handling and processing. This can involve tasks such as conveying, mixing, or agitating materials within a manufacturing or processing system.
Question 2: What factors influence the selection of materials for a turner kufe?
Material selection for a turner kufe is dictated by operational conditions. Factors include anticipated loads, operating temperatures, the nature of the materials being processed, and desired lifespan. Materials must exhibit adequate strength, wear resistance, and resilience to the specific working environment.
Question 3: How does the design of a turner kufe affect its performance?
Turner kufe design significantly impacts its performance. Key design elements include the geometry of rotating parts, bearing selection, and structural integrity. Optimized design minimizes friction, vibrations, and wear, maximizing efficiency and lifespan.
Question 4: What are the essential maintenance considerations for a turner kufe?
Regular maintenance is crucial for optimal turner kufe performance. This includes periodic inspections, lubrication, and component replacements based on pre-determined schedules or operational hours. Preventive maintenance minimizes downtime and extends the component's operational life.
Question 5: How does integration of a turner kufe within a larger system impact overall efficiency?
Proper integration is paramount. Compatibility with existing machinery, power systems, and control mechanisms ensures smooth workflow and maximized efficiency. Careful planning and execution during installation minimize disruptions and maximize output.
In summary, understanding the design, operational principles, and maintenance procedures for turner kufes is vital for optimal performance in industrial settings. Careful consideration of these elements contributes to a more efficient and sustainable process.
Next, we will delve into specific applications and case studies showcasing the effective use of turner kufes within various industries.
Conclusion
This analysis explores the multifaceted nature of the turner kufe, a crucial component in various industrial applications. Key aspects, including design, material selection, rotational dynamics, control mechanisms, support systems, maintenance procedures, and integration strategies, were examined. The study highlights the critical role of each element in ensuring reliable operation, maximized efficiency, and prolonged lifespan of the component. Factors such as appropriate material selection to withstand operating conditions, meticulous design for optimal rotational speed and control, and proactive maintenance schedules contribute significantly to operational effectiveness. The analysis underscores the importance of comprehensive planning when integrating the turner kufe into larger industrial systems. Effective integration is crucial for minimizing production disruptions and maximizing overall output.
The successful deployment of a turner kufe hinges on a thorough understanding of its operational principles and integration requirements. Optimizing the component's performance through meticulous design, careful selection of materials, and proactive maintenance procedures ultimately minimizes downtime and maximizes output. The integration phase demands meticulous attention to mechanical compatibility, power and control systems, and workflow optimization. This in-depth examination emphasizes that the turner kufe's effectiveness is directly linked to comprehensive understanding and strategic application within specific industrial processes. Future research could focus on advanced control systems and predictive maintenance techniques to further enhance the reliability and efficiency of this critical component.
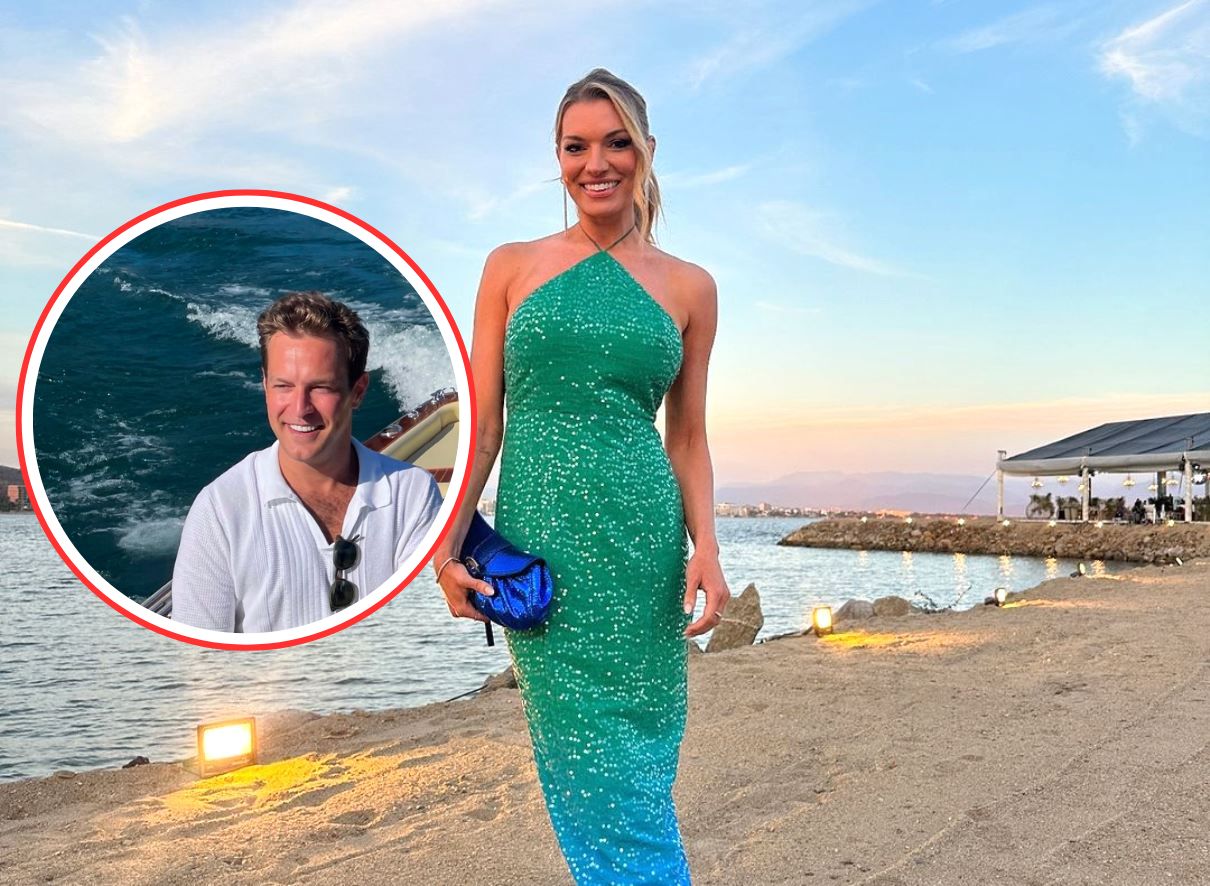
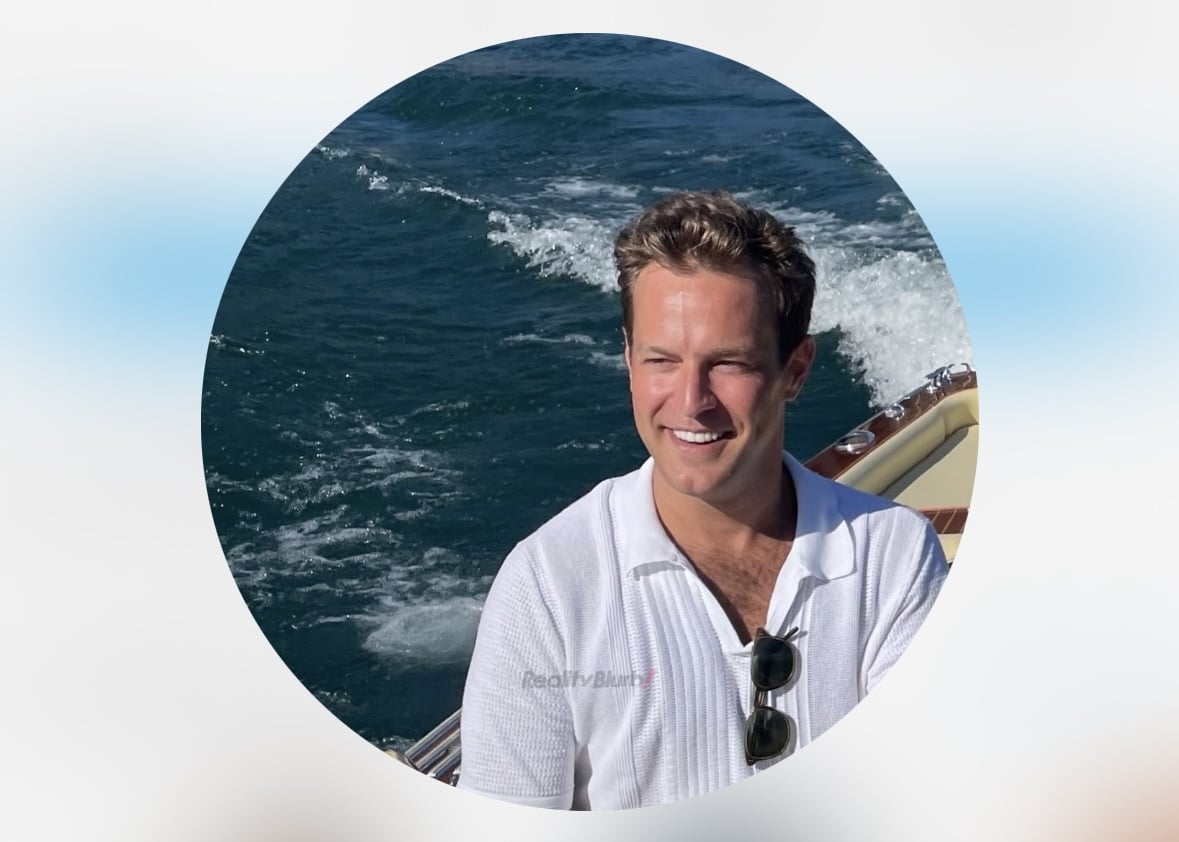
