How do you optimize resource flow in Factorio? This article explores techniques for extending production chains.
Extending production chains in Factorio is a crucial aspect of maximizing output and efficiency. It involves connecting multiple production stages, like ore processing, crafting, and assembly, in a coordinated manner. This creates a continuous flow of resources, minimizing bottlenecks and maximizing output. A well-designed extended production pipeline can dramatically increase the rate at which desired items are produced. For example, if you need a high volume of circuit boards, extending the circuit board production chain by adding more assemblers, and a properly sized supply of components, results in a consistent supply of finished goods. This process often involves careful consideration of resource input, processing steps, and output storage.
The benefit of properly configured production pipelines is significant. Efficient resource management leads to faster overall production, reducing downtime and increasing profits (in-game). A well-organized production chain allows for quick responses to changing demands, a crucial element of advanced gameplay. Properly extending production lines is essential for players facing increasingly complex and demanding objectives, particularly in multiplayer scenarios. It is a significant component of optimizing game performance for both single-player and multiplayer settings. Historical data from Factorio players consistently shows a strong correlation between advanced pipeline extension strategies and high-score runs.
Let's dive into the mechanics of creating robust and efficient production lines in Factorio, exploring strategies for streamlining your resource flow and maximizing output. We will cover specific methods for design, including balancing production and consumption, predicting demand, and managing inventory.
Pipeline Extension in Factorio
Optimizing resource flow in Factorio is crucial for efficient production. Extending production pipelines requires careful consideration of several key elements.
- Resource Management
- Demand Forecasting
- Throughput Optimization
- Production Balancing
- Inventory Control
- Modular Design
- Chain Redundancy
Effective pipeline extension hinges on meticulous resource management, anticipating demand fluctuations, and optimizing throughput. Production balancing is key, ensuring consistent resource flow. Careful inventory control prevents bottlenecks. Modular designs allow for flexibility and scaling, while redundant chains provide safety nets against unexpected disruptions. For example, a well-designed pipeline for circuit boards will efficiently handle demand fluctuations by connecting ore processing, circuit component production, and final assembly stages in a balanced flow. Maintaining a consistent supply chain prevents potential production slowdowns and maximizes output.
1. Resource Management
Effective resource management is fundamental to successful pipeline extension in Factorio. A well-structured pipeline depends entirely on a steady and reliable supply of raw materials. Insufficient or inconsistent resource provision will inevitably lead to bottlenecks and reduced throughput. This principle is applicable beyond Factorio; the efficient management of materials is crucial for production in any manufacturing or industrial setting. For instance, if a pipeline for producing circuit boards relies on a sporadic and inadequate supply of copper ore, the circuit board production line will be crippled, regardless of how optimized the remaining stages may be. Resource management, therefore, acts as a crucial prerequisite for a well-functioning extended production pipeline.
Resource management encompasses a comprehensive approach to resource acquisition, processing, and allocation. This includes establishing reliable supply chains for raw materials, optimizing processing methods, and establishing efficient storage and distribution mechanisms. In the context of Factorio, players must consider not just the immediate needs of their current production line, but also the long-term requirements. This foresight involves calculating resource demands, anticipating potential shortages, and planning for adequate storage capacity. Effective inventory management helps alleviate unexpected production halts due to material shortages. Consequently, a properly managed resource pipeline will allow for more robust and flexible production chains, capable of adapting to fluctuating demands and unexpected events.
In summary, robust resource management is an indispensable component of effective pipeline extension in Factorio. The ability to maintain a consistent flow of resources throughout the entire production chain is paramount to achieving high throughput. Failing to adequately manage resources will invariably disrupt the pipeline, resulting in diminished output and inefficiencies. By understanding and implementing effective resource management strategies, players can optimize their Factorio production and achieve a higher level of output and productivity. This principle of resource management extends beyond the virtual world, offering valuable insights into the fundamental elements of operational efficiency in various industries.
2. Demand Forecasting
Accurate demand forecasting is crucial for optimizing production pipelines in Factorio. Anticipating future needs for resources and products allows for proactive adjustments, preventing bottlenecks and maximizing output. A properly predicted demand translates into streamlined resource allocation and efficient production, reducing idle time and maximizing output. Failure to accurately predict future demands can lead to inefficient use of resources and ultimately affect overall production performance.
- Forecasting Methodology
Strategies for demand forecasting in Factorio involve analyzing historical production data, identifying patterns, and predicting future trends. This analysis incorporates factors like current production rate, anticipated growth, and seasonal or event-driven variations in demand. Sophisticated methods often employ mathematical models, historical data, and qualitative factors such as changes in player strategy or game mechanics. For example, recognizing a steady rise in circuit board production in response to technological advancements might prompt a proactive expansion of the circuit board production pipeline to meet the projected demand.
- Impact on Production Efficiency
Precise demand forecasting allows production lines to be sized appropriately. Over-provisioning can lead to excess inventory and wasted resources, while under-provisioning results in shortages and production delays. By aligning production capacity with predicted demand, resources are utilized more effectively, minimizing bottlenecks and maximizing throughput. This is crucial for optimizing in-game economic growth and success in achieving various in-game objectives. For instance, a sufficiently anticipated increase in demand for circuit boards permits players to invest resources efficiently and construct the necessary infrastructure without a sudden, costly scramble to meet the unforeseen demand.
- Pipeline Adaptation to Change
Effective demand forecasting allows the Factorio production pipeline to adjust dynamically to changing conditions. Foreseeing fluctuating demand, whether due to seasonal variations or game events, allows for timely adjustments to production. This flexibility minimizes disruption and ensures continued output even in response to fluctuating demand. This adaptable approach can be compared to supply chain management strategies in real-world manufacturing, emphasizing preparedness for unexpected fluctuations in demand.
- Resource Allocation Strategies
Accurate demand forecasting facilitates effective resource allocation. By proactively understanding the future demands of the production pipeline, players can strategically allocate resources, minimizing waste and ensuring a steady supply of materials. This planning translates to a balanced allocation of resources according to predicted needs and prevents bottlenecks in the system. Properly allocating resources allows players to quickly address potential problems and efficiently manage various production areas.
In essence, accurate demand forecasting forms the bedrock of a robust production pipeline in Factorio. By anticipating future demands, players optimize resource allocation, enhance production efficiency, and mitigate disruptions, ultimately achieving a sustainable and profitable in-game economy. This skill translates effectively to a wide variety of situations in other disciplines involving the management of resources.
3. Throughput Optimization
Throughput optimization, a critical component of efficient production systems, directly impacts the effectiveness of pipeline extension in Factorio. Maximizing the rate at which resources flow through the production chain is paramount to achieving high output. Strategies for throughput optimization are crucial for expanding and maintaining successful production pipelines. This section explores key facets of throughput optimization within the context of Factorio's production systems.
- Balancing Production Stages
Maintaining a consistent flow of resources across all production stages is essential. An imbalance in throughput between any production stage can choke the entire pipeline, leading to bottlenecks. Ensuring that each stage of the production pipelinefrom resource extraction to final product assemblyprocesses resources at a rate comparable to the next stage is a critical factor. For instance, if ore processing is too slow to keep up with smelter capacity, the pipeline will be constrained, and subsequent stages will suffer. This concept aligns with principles of supply chain management, where maintaining a smooth flow of materials and goods across the entire production chain is essential.
- Optimizing Resource Allocation
Optimizing the allocation of resources within each production stage is essential for maximizing throughput. Efficiently matching the capacity of production units to the rate of resource availability minimizes idle time and maximizes overall output. This involves carefully evaluating the resources required for each step, matching production rates of different stages, and using tools to estimate and manage resource needs. A production process characterized by a consistent supply of necessary resources throughout the entire process is key to maintaining efficient throughput.
- Minimizing Bottlenecks
Identifying and mitigating bottlenecks in the production pipeline is fundamental to throughput optimization. A bottleneck anywhere in the pipeline slows down the entire process, significantly reducing efficiency and effectiveness. This necessitates regular monitoring of resource flow and production rates, enabling rapid identification of and corrective actions to address potential issues. For instance, a shortage of crafting stations at a given stage would restrict throughput, requiring either increased capacity at that stage or adjustments elsewhere in the pipeline.
- Implementing Buffering Strategies
Implementing appropriate buffering strategies to account for fluctuations in production rates is crucial for maintaining throughput. Buffers provide temporary storage for resources, absorbing variability and smoothing out irregularities. By strategically introducing buffer storage between production stages, the system becomes more resilient to minor disruptions in workflow or resource supply. This strategy is critical to managing unpredictable occurrences and maintaining optimal flow.
These facets demonstrate how throughput optimization is deeply interwoven with effective pipeline extension. By addressing resource allocation, bottlenecks, and variability, players can optimize the flow of resources through their extended production pipelines, ultimately maximizing their output and efficiency within Factorio. This strategy, drawing parallels to manufacturing processes in the real world, emphasizes the need for careful planning and continuous monitoring in achieving optimal throughput.
4. Production Balancing
Production balancing is fundamental to effective pipeline extension in Factorio. Maintaining a consistent flow of resources throughout the entire production chain requires careful coordination between different production stages. Imbalances in resource processing or product output can create bottlenecks, significantly hindering overall efficiency. This section explores the crucial role of production balancing in creating robust and optimized production pipelines.
- Matching Production Rates
A primary aspect of production balancing is ensuring that each stage of the production pipeline can effectively handle the output of the preceding stage. If one stage produces resources faster than the subsequent stage can consume them, bottlenecks will occur. Conversely, if a stage is slower than the previous one, it becomes a bottleneck, restricting the overall production rate. This concept is analogous to assembly lines in real-world manufacturing, where maintaining a steady pace across all stations is vital for optimal output.
- Optimizing Resource Allocation
Equitable allocation of resources across production stages is crucial for balancing the pipeline. Insufficient resources at any stage create a bottleneck. Determining the optimal allocation of resources requires understanding the resource demands of each stage and the necessary materials to keep the pipeline moving. This involves careful consideration of material usage at every step to ensure production stays balanced.
- Preventing Bottlenecks
A critical aspect of production balancing is proactively identifying and mitigating potential bottlenecks. Anticipating resource constraints or processing capacity limitations is key to preventing disruptions in workflow. Monitoring and analysis of production rates at different stages allows for targeted adjustments in resource allocation or capacity upgrades. Identifying and resolving bottlenecks maintains a stable and efficient production pipeline.
- Adaptability and Scalability
Production balancing must consider adaptability and scalability. Adjustments to production rates based on fluctuating demands are necessary to maintain a stable pipeline. Production balancing facilitates the adaptation of production strategies to changing resource availability and market demands. Expanding the pipeline to accommodate increased production demands requires well-structured modifications to ensure balanced processing at all stages.
In conclusion, production balancing is not a one-time task but an ongoing process. By understanding the interdependencies between different production stages, meticulously managing resource allocation, and proactively identifying and resolving bottlenecks, players can create highly efficient and adaptable production pipelines in Factorio. This approach to production balancing translates to substantial improvements in output and overall game progression.
5. Inventory Control
Effective inventory control is inextricably linked to successful pipeline extension in Factorio. Maintaining appropriate stock levels of raw materials and finished goods is critical for preventing bottlenecks and ensuring a consistent flow of resources through the production system. Without proper control, the production pipeline can be disrupted by shortages or surpluses, leading to decreased output and wasted resources. Efficient inventory management is essential for maximizing production throughput and overall efficiency.
- Optimizing Stock Levels
Maintaining optimal stock levels is fundamental. Excessive inventory ties up resources and incurs storage costs, while insufficient inventory leads to production halts and lost output. A delicate balance must be struck to ensure a continuous supply of materials without unnecessary accumulation. This principle applies to various manufacturing and supply chain management scenarios, highlighting the importance of precise forecasting and demand analysis in determining optimal stock levels.
- Real-Time Tracking
Real-time tracking of inventory levels is crucial for proactive management. Systems for monitoring stock levels in real time allow for timely adjustments to production schedules and resource allocation. This capability enables the identification of potential shortages or surpluses early on, allowing for immediate corrective actions to be taken before bottlenecks arise. Sophisticated inventory management software allows for this real-time visibility, providing crucial data for timely adjustments in production planning and minimizing interruptions in workflow.
- Efficient Storage and Distribution
Efficient storage and distribution systems are vital for smooth resource flow. Organized storage facilitates quick retrieval of materials, minimizing downtime during production. Efficient distribution systems ensure timely delivery of resources to various production stages. Minimizing storage space is essential, and storage systems must be configured to allow for quick retrieval of resources as needed. This directly impacts throughput within the production pipeline, ensuring the timely availability of components.
- Predictive Modeling
Predictive modeling plays a significant role in optimizing inventory control. By analyzing historical production data and anticipating future demands, accurate inventory forecasts can be developed. This allows for proactive adjustments in production schedules and resource procurement, minimizing potential disruptions and maximizing efficiency. Such modeling techniques are crucial for long-term planning and ensure that the production system can adapt effectively to changing circumstances and demands.
Implementing robust inventory control mechanisms directly contributes to successful pipeline extension in Factorio. By optimizing stock levels, utilizing real-time tracking, creating efficient storage and distribution systems, and employing predictive modeling, players can mitigate disruptions, streamline resource flow, and maximize production throughput. This holistic approach mirrors best practices in supply chain management and highlights the critical role of inventory control in achieving optimized output in complex manufacturing environments.
6. Modular Design
Modular design significantly enhances the extensibility and adaptability of production pipelines in Factorio. A modular approach allows for the creation of independent, self-contained units within the larger pipeline. These units, when properly interconnected, form a cohesive production chain. This modularity facilitates scalability and modification, making the pipeline more adaptable to changes in production needs or resource availability. For instance, a modular design for producing circuit boards could involve separate modules for copper ore processing, circuit component assembly, and final circuit board assembly. Modifying or expanding one module, such as adding more circuit board assemblers, does not necessitate a complete overhaul of the entire pipeline. This approach mirrors real-world manufacturing where modular designs allow for flexible customization and rapid response to evolving demands.
The practical significance of modular design is multifaceted. Firstly, it simplifies maintenance and troubleshooting. If a problem arises in one module, the impact on the entire pipeline is minimized. Replacement or repair of a faulty module is isolated, reducing downtime and accelerating the restoration of production. Secondly, modularity promotes scalability. Adding new modules or replicating existing ones allows for a proportional increase in output without significant changes to the existing structure. For example, doubling the output of copper ore processing could involve simply adding a second, modular ore processing unit. This contrasts with a non-modular design, where expanding capacity often necessitates a complete redesign and reconstruction of the entire pipeline. Thirdly, modularity fosters flexibility and allows for tailoring the production process to specific game requirements. Players can design and implement multiple production chains based on their needs and priorities, thereby customizing their strategy and optimizing resource utilization.
In summary, modular design provides the critical flexibility and adaptability necessary for successful pipeline extension in Factorio. This approach significantly improves the resilience and scalability of production chains. The ability to isolate and modify individual modules minimizes downtime, simplifies maintenance, and enhances overall efficiency. By adopting a modular design strategy, players can build more robust, adaptable, and ultimately more effective production systems, mirroring the benefits of modular design across various real-world industrial settings. This modular approach is crucial for achieving highly optimized and responsive manufacturing processes in both virtual and physical realms.
7. Chain Redundancy
Chain redundancy, a crucial element in extended production pipelines within Factorio, introduces backup systems to mitigate the impact of failures. A single point of failure can cripple a production line, causing significant delays or complete halt in output. Implementing redundant systems ensures a continuous flow of resources even when a part of the pipeline experiences a problem. The concept of redundancy is paramount in diverse sectors, from power grids to critical infrastructure, and exemplifies the importance of robust planning and preparation to prevent disruptions.
In Factorio, this translates to having alternative pathways for resources to flow. For example, a redundant ore-processing system would involve multiple miners, smelters, and other processing units. If one miner malfunctions, the system can still function using the remaining miners. If one smelter breaks down, the alternative path for materials allows production to continue using the available replacement resources. This redundancy ensures continued throughput when unforeseen events impact the primary chain. This concept extends to later stages of processing, like assembly and refinement, adding safety measures to production lines. The strategic placement of backup components, combined with well-defined pathways, creates a more resilient and robust production pipeline. This approach directly addresses the vulnerability to downtime often associated with centralized systems. Redundancy minimizes the impact of equipment malfunctions, ensuring the production pipeline continues functioning effectively. Examples can be seen in transportation networks and supply chains of many industries.
The practical significance of understanding chain redundancy within Factorio's extended production pipelines is substantial. It highlights the importance of resilience design principles in creating sustainable and high-output systems. A well-designed redundant system mitigates risk, maintaining continuous production despite potential issues. A player with a well-planned, redundant production line not only secures a dependable supply of goods but also reduces the risk of costly downtime caused by equipment failure. This understanding extends to many real-world situations, emphasizing the importance of robustness in design and operations.
Frequently Asked Questions
This section addresses common queries regarding extending and optimizing production pipelines in Factorio, focusing on effective resource management and maximizing output.
Question 1: What are the initial steps for creating an effective production pipeline?
Answer 1: The foundational step involves meticulous resource management. Assess available raw materials and production capacity. Calculate the throughput rate required for the desired output. Thorough planning is crucial, identifying bottlenecks and points of potential inefficiency in the resource flow from input to finished product.
Question 2: How can I anticipate fluctuations in resource demand?
Answer 2: Historical data analysis and predictive modeling are vital. Analyzing past production rates and correlating them with game events or seasonal changes can provide insights. Anticipating demand changes allows for proactive adjustments to production levels and resource allocation, preventing shortages or surpluses.
Question 3: How do I effectively balance production rates across different stages?
Answer 3: Maintaining a consistent throughput across all production stages is key. Calculate the processing rate for each step and match it with the succeeding stages. Ensure no single stage becomes a bottleneck, slowing the entire pipeline. Optimal allocation of resources to each stage is critical to a balanced system.
Question 4: What strategies can I use to mitigate production bottlenecks?
Answer 4: Identify bottlenecks by monitoring resource flow and production rates. Implement buffering strategies (additional storage) between stages. Consider increasing processing capacity at the bottleneck stage or adjusting the production rate upstream. Proactive identification and management of bottlenecks minimize downtime and maintain throughput.
Question 5: How can I ensure my pipeline is adaptable to changes in game progression?
Answer 5: Employ a modular design approach. Create independent production units (modules). This isolates bottlenecks, simplifying maintenance, and allowing for easy scaling. Modular design enables flexibility to add or remove units to adapt to evolving resource needs or challenges.
Understanding these principles is key to building a robust and efficient production pipeline in Factorio, maximizing output and minimizing waste. This careful management leads to greater success in achieving desired in-game outcomes.
Let's now explore specific strategies for implementing these concepts in practice.
Conclusion
This article explored the multifaceted aspects of optimizing resource flow in Factorio, emphasizing the crucial role of extended production pipelines. Key considerations include meticulous resource management, accurate demand forecasting, optimized throughput, balanced production across stages, effective inventory control, modular design principles, and the strategic implementation of chain redundancy. Each element plays a critical role in establishing a robust and efficient system, maximizing output and minimizing downtime. The successful extension of production pipelines hinges on a deep understanding of these interconnected principles.
The principles discussed offer a framework for crafting sophisticated and adaptable production systems. Proficient application of these techniques not only ensures higher output but also enhances overall in-game economic performance and resource management skills. Further exploration into specific strategies and techniques for implementation can lead to even more optimized production systems, further demonstrating the significance of understanding these principles in achieving success in the Factorio game environment.

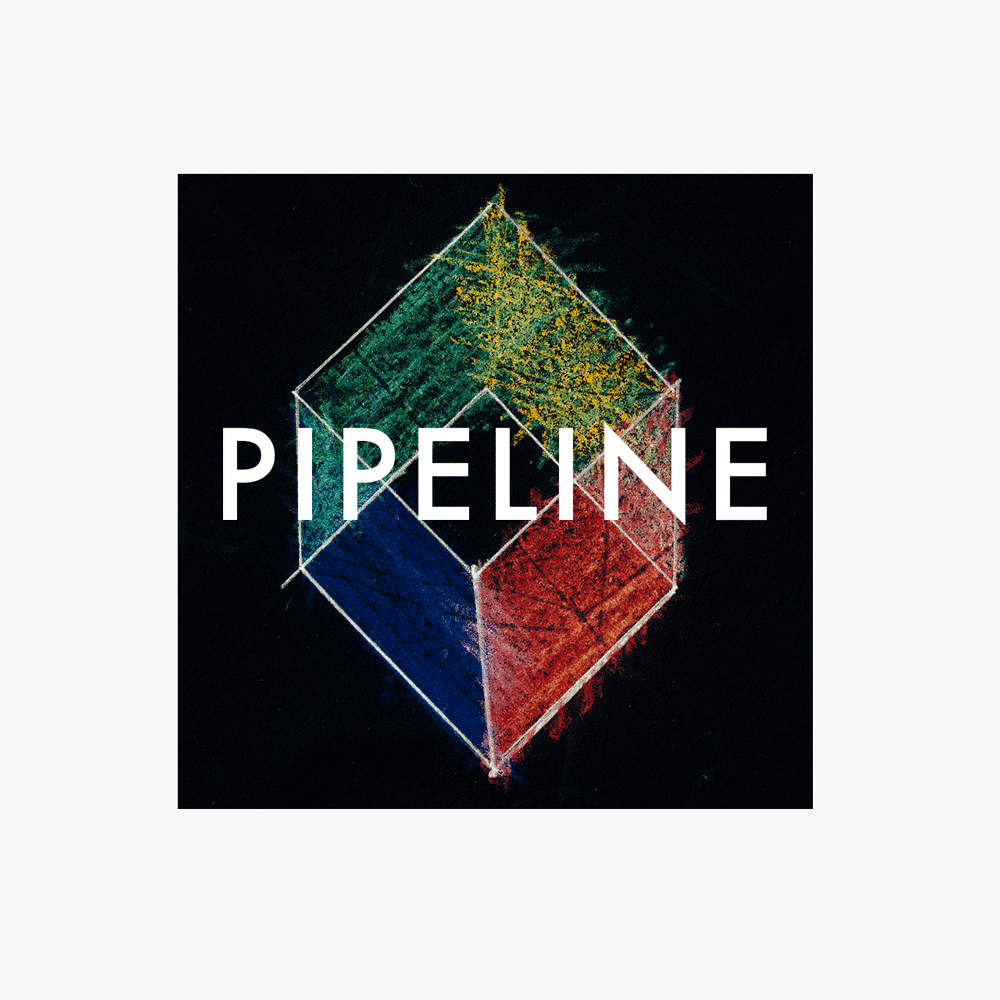
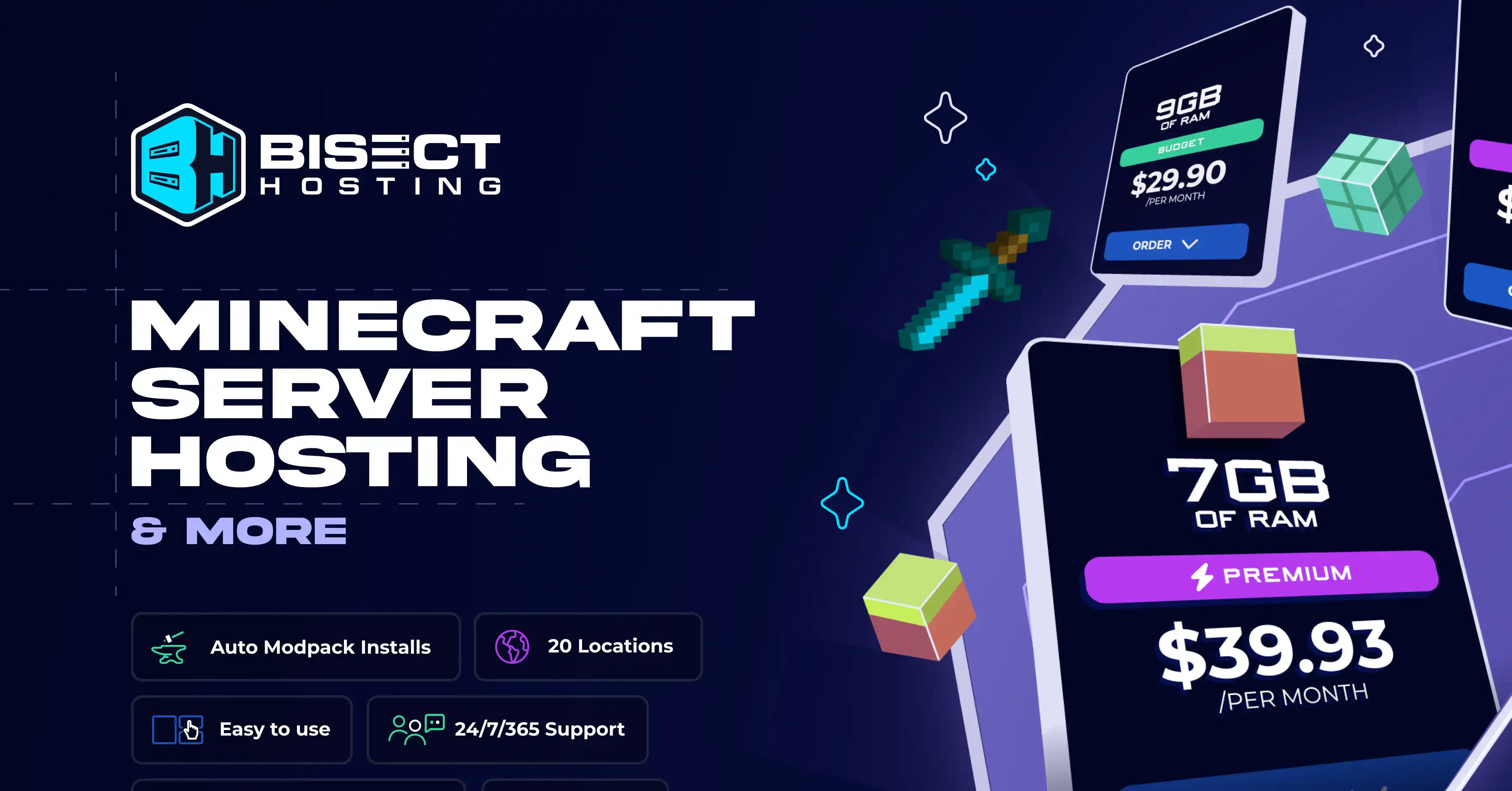