When production lines in Factorio become overloaded, how do they impact overall efficiency? A critical bottleneck in Factorio production, overextended conveyance systems are a key issue in game optimization.
Overburdened production chains, where items flow through processing stations faster than they can be handled, represent a common challenge in Factorio. This situation often arises from insufficient processing capacity at critical junctions, or from an imbalance in the speed of production and transportation. For instance, a fast-producing copper smelter feeding into a slower-working circuit board assembler can create a choke point, backing up the entire pipeline and stalling progress. A similar scenario may arise when the volume of output exceeds the capacity of the connecting belts or train lines. The result is a standstill, reducing overall output and impacting resource allocation.
Optimizing the flow of resources within Factorio's industrial system is crucial for maximizing production and minimizing waste. An efficient system minimizes downtime and bottlenecks, leading to greater economic returns in game terms. Understanding and correcting overextended conveyance systems is paramount for reaching production goals. This requires careful planning, considering not just the immediate processing steps but also the entire chain of production from raw materials to finished goods. The focus should be on balancing throughput across all components, ensuring a consistent and continuous flow, without overloading any section.
Let's delve into strategies for tackling production imbalances, examining various methods for upgrading conveyor belts, train lines, and processing facilities to prevent this issue. Furthermore, we will investigate the impact of introducing automation or advanced production methods on throughput and efficiency.
Pipeline Overextended Factorio
Optimization of resource flow in Factorio is paramount. Understanding and mitigating pipeline overextension is crucial for maximizing production output and minimizing bottlenecks.
- Resource imbalance
- Conveyor capacity
- Processing speed
- Production rate
- Automation levels
- Storage capacity
- Logistics design
Resource imbalance and insufficient conveyor capacity often lead to bottlenecks. Processing speed is a critical factor, if production surpasses the rate of processing or transportation, overextension ensues. Production rate must be balanced with downstream capabilities and storage limits. Automation levels significantly impact the handling rate; poorly optimized automation can easily lead to overextension. Ensuring adequate storage capacity prevents material accumulation and downstream congestion. Finally, the optimal logistics design is pivotal in preventing congestion and maximizing throughput. For instance, a rapid-producing copper smelter connected to a slow circuit board assembler necessitates intermediate storage or speed upgrades to prevent an overextended pipeline.
1. Resource Imbalance
Resource imbalance is a fundamental driver of pipeline overextension in Factorio. Disparate production rates of raw materials and finished goods create a strain on the system's capacity. This imbalance directly impacts the flow of resources through the production pipeline, leading to bottlenecks and reduced overall efficiency.
- Disparate Production Rates
Significant disparities in the output of different resources often lead to imbalances. For example, if a player produces copper ore at a high rate but lacks the capacity to process it, the excess raw material will back up the production pipeline. This bottleneck affects subsequent stages that rely on processed copper, leading to a domino effect of delays. Similarly, an abundance of circuit boards with insufficient demand for them can also lead to overextension.
- Unbalanced Production Chains
A mismatch between the production rates of various stages in a production chain is a key contributor. If one stage produces components at a faster pace than subsequent stages can utilize them, a buildup of intermediate products occurs, eventually causing the pipeline to become congested. A scenario where the rate of raw material production greatly exceeds the capacity of the processing plants is a prime example.
- Demand Fluctuations
Unpredictable or fluctuating demand for specific resources can exacerbate resource imbalances. If a player ramps up production of a particular item suddenly, but the supply chain for that item cannot keep pace, the production pipeline will overextend. This scenario demands flexible production planning to accommodate such variations.
- Lack of Forecasting and Planning
Improperly forecasted resource demands and a lack of comprehensive production planning often result in severe imbalances. Without a strategic overview of the overall production chain and anticipated resource needs, players can rapidly find themselves facing an overextended pipeline. A clear understanding of future demand and proactive measures to adjust production are crucial.
In summary, resource imbalance significantly contributes to pipeline overextension in Factorio. Understanding and mitigating these imbalances through meticulous planning, balanced production rates, and adaptable strategies is crucial for optimizing the overall production system and maximizing efficiency.
2. Conveyor Capacity
Insufficient conveyor capacity is a primary cause of pipeline overextension in Factorio. The capacity of the transport system directly affects the rate at which resources can be moved through the production chain. When this capacity is insufficient to handle the volume of items being produced, bottlenecks emerge, leading to a backlog of resources and hindering overall production. This issue is prevalent when raw materials, components, or finished goods accumulate in transit areas, preventing the smooth flow of the production pipeline.
- Impact of Conveyor Belt Limitations
Conveyor belts have a finite capacity. When the volume of items exceeds this capacity, the system becomes overloaded. Items pile up, slowing down the entire production line. This is a common problem when attempting to transfer goods between stations that process items at vastly different rates. A fast-producing smelter connected to a slower circuit board assembly line creates a bottleneck. In such scenarios, upgrading conveyor belts to a higher capacity or strategically adding intermediate storage facilities becomes necessary to prevent overextension.
- Relationship with Production Rates
The capacity of conveyor belts must match the production rate of the stations they connect. A production chain with high output requires correspondingly high conveyor capacity to avoid accumulating inventory and overextending the pipeline. If the production output far surpasses the conveyor's capacity, the system quickly becomes congested, reducing overall productivity. An inadequate conveyor system fundamentally limits production rate, regardless of processing speed at other stations.
- Effect of Automation and Specialization
Automation often increases production rates. If conveyor capacity does not increase proportionally, the result is an overextension of the production pipeline. Furthermore, specialized production lines, which often require high throughput, are especially vulnerable to capacity issues. For example, if a conveyor system cannot handle the output of an automated mining station feeding into a complex processing system, the production pipeline will be overextended and inefficient.
- Strategic Placement and Redundancy
Careful placement of conveyor belts and the inclusion of redundancy in the transportation system is vital to mitigate the risk of overextension. The placement should consider the volume of items flowing between stations. Redundancy, in the form of additional conveyor belts or alternative pathways, can mitigate the impact of bottlenecks. Having alternative paths or storage areas to accommodate temporary production surges can dramatically improve system stability.
In conclusion, adequate conveyor capacity is an essential aspect of a smoothly operating Factorio production pipeline. Addressing issues related to conveyor capacity is crucial for preventing pipeline overextension, optimizing resource flow, and maximizing production efficiency. Ignoring these factors inevitably leads to bottlenecks, reduced throughput, and substantial loss of output in the game.
3. Processing Speed
Processing speed plays a critical role in preventing pipeline overextension in Factorio. A mismatch between the rate of production and the rate at which items are processed leads to bottlenecks and congestion within the production pipeline. When processing speed is insufficient to accommodate the volume of incoming items, resources accumulate, slowing down the entire system. This bottleneck not only reduces overall throughput but also affects the efficient allocation of resources across the entire factory. A fast production line feeding into a slow processing station is a prime example of a situation leading to pipeline overextension.
The connection is direct: if items are produced faster than they can be processed, the pipeline becomes congested. Consider a copper smelter producing output at a high rate, but the circuit board assembler downstream has a lower processing capacity. This mismatch generates a queue of unprocessed copper, ultimately backing up the entire production chain. Real-world examples illustrate this principle. In manufacturing, assembly lines with imbalances in processing speeds face similar challenges. Maintaining a consistent processing speed throughout the entire chain minimizes congestion and maximizes throughput. Understanding this relationship allows for strategic placement of resources to improve factory flow and output.
In essence, processing speed is a critical component in maintaining a healthy production pipeline. By ensuring processing speeds are balanced across the entire production chain, minimizing delays and maximizing efficiency become attainable goals. This understanding allows for proactive optimization of the factory layout and resource allocation, leading to a more productive and stable Factorio operation.
4. Production Rate
Production rate directly influences the likelihood of pipeline overextension in Factorio. A misalignment between the rate at which resources are produced and the rate at which they can be processed, transported, or consumed creates bottlenecks. If production outpaces the system's capacity to handle the output, the pipeline becomes overextended. This phenomenon is analogous to assembly lines in manufacturing, where imbalances in production and processing can lead to delays and reduced efficiency. High production rates, if not balanced with appropriate processing and transportation capacity, are a primary cause of the problem.
Maintaining a harmonious balance between production rates across the entire chain is crucial for preventing overextension. For instance, an automated mining operation producing raw materials at a rapid pace needs matching processing and transportation capacity downstream. A fast-producing smelter feeding into a slower circuit board assembler creates a bottleneck, leading to a buildup of unprocessed materials. This bottleneck impacts the entire pipeline. Similarly, an excessive rate of manufacturing finished goods beyond current demand will lead to an overextended pipeline and potential loss of resources. Planning and adjusting production rates to match the capacity of the downstream operations are essential preventative measures. Strategies to regulate production, like introducing buffering, implementing adjustable automation settings, or prioritizing production based on current demand, are vital to maintain a healthy production pipeline. Consider real-world examples of production lines; bottlenecks often arise due to uneven production rates in various stages, causing a cumulative slowdown. Proactive management of production rates is a key component in optimizing resource flow and preventing pipeline overextension.
In conclusion, production rate is a critical determinant in Factorio's pipeline health. Fluctuations in production rates significantly impact resource flow and contribute to pipeline overextension. Understanding the connection between production and pipeline efficiency is paramount for effective factory design, resource allocation, and optimal resource output. Addressing imbalances in production rates is crucial for maintaining a smooth and productive workflow in Factorio. Implementing strategies for managing production rates will contribute to a more efficient and optimized industrial system, preventing inefficiencies and maximizing returns.
5. Automation Levels
Automation levels significantly influence the risk of pipeline overextension in Factorio. Increased automation often leads to higher production rates, but without careful consideration of the downstream system's capacity, this can exacerbate bottlenecks. Improperly balanced automation can lead to an accumulation of resources at certain points in the production line, effectively overwhelming the transport mechanisms and causing the pipeline to become overextended. Understanding the intricate relationship between automation and pipeline health is key to optimizing factory design and maximizing efficiency.
- Impact of Automated Production Rates
Automated systems, by their nature, often produce goods at a significantly faster rate than manual processes. This speed increase can rapidly overwhelm subsequent stages in the pipeline if the processing, transport, or storage capacity cannot keep pace. For instance, an automated mining station producing raw materials at a high rate, if not connected to an equally capable processing and transportation system, will quickly cause an accumulation of raw materials. This accumulation stresses the pipeline, reducing efficiency and creating a bottleneck.
- Effect of Automation on Conveyor Capacity Requirements
Automation's effect on conveyor capacity is substantial. Increased automation often leads to greater throughput demands. Conveyor belts, trains, and other transportation elements need to be appropriately scaled to manage the increased volume of goods flowing through the pipeline. If the automation increases production without corresponding improvements in the transport network, the system will become overextended and create inefficiencies. Failure to properly upgrade transportation infrastructure to match automation will invariably result in pipeline overextension. For instance, a high-output, automated smelting system will need substantially more transport capacity to handle the increased flow compared to a similar system with lower automation. A failure to account for this will quickly lead to bottlenecks.
- Balancing Automation with Processing Capacity
Automation often focuses on increasing output. However, a significant disparity in processing speed between automated stations and other stages in the production line will inevitably lead to a backlog. If the automated production surpasses the processing capacity of subsequent stations, the pipeline is bound to become overextended. A strategic approach is required to ensure a well-balanced production cycle from automated extraction to final assembly, ensuring each segment has adequate processing power to handle the volume of input. This balanced approach is critical to prevent pipeline overextension. This includes strategically implementing buffering systems, which can momentarily store intermediate products to even out throughput.
- Strategic Use of Automation to Mitigate Bottlenecks
While automation can increase production rates, strategic use can also mitigate potential pipeline overextension. Automation isn't inherently problematic; rather, the key is in recognizing automation's impact on downstream processes and adjusting accordingly. For example, introducing automated sorting or buffering systems can address fluctuations in production and processing capacity to a degree. Well-timed and strategically planned automation installations can proactively prevent future overextension. This proactive planning allows the system to evolve with growing production needs, ensuring continuous optimal efficiency.
In conclusion, automation levels significantly impact the risk of pipeline overextension. Careful planning and consideration of the entire production chain, including transport and processing capacity, are crucial when incorporating automation to optimize factory design and resource flow. Neglecting this aspect will often result in bottlenecks and reduced overall efficiency in Factorio.
6. Storage Capacity
Adequate storage capacity is critical for mitigating pipeline overextension in Factorio. Insufficient storage acts as a bottleneck, disrupting the flow of resources through the production chain. Accumulation of unprocessed materials upstream creates pressure on the system, leading to delays and ultimately hindering overall production output. The interplay between production, processing, and storage directly impacts the health of the production pipeline.
- Buffering and Fluctuations in Production/Processing
Storage acts as a buffer between varying production and processing speeds. When production outpaces processing, a sufficient storage capacity allows for temporary accumulation without disrupting downstream stages. Conversely, if processing speed surpasses production, adequate storage prevents a shortage of raw materials. This buffering effect smooths out variations in throughput, preventing abrupt stops and starts in the production pipeline. A robust storage system effectively manages these fluctuations, maintaining a consistent flow of resources through the factory. Real-world examples of manufacturing processes include intermediate storage in electronics assembly and warehousing in general. These examples demonstrate how buffering minimizes the impact of fluctuations.
- Impact of Insufficient Storage
Insufficient storage directly exacerbates pipeline overextension. A lack of storage leads to an immediate buildup of resources at points within the pipeline. This accumulation creates bottlenecks, slowing or halting production at downstream stations. It also forces the player to prioritize certain stages, potentially disrupting an otherwise well-balanced production chain. Consider a scenario with high-speed mining but insufficient storage for processed ores. The production pipeline becomes clogged, impacting subsequent stages involving further processing.
- Strategic Placement and Optimization of Storage
Strategic placement of storage facilities is crucial for optimizing resource flow. Positioning storage units between stages with different processing rates allows for smoother flow. For example, placing storage between a fast-producing smelter and a slower circuit board assembly line allows the smelter to operate without being constrained by the slower downstream stage. Optimizing this placement maximizes throughput. This is comparable to strategically located warehouses in real-world supply chains, allowing for efficient material handling between production and distribution.
- Relationship between Storage and Overall Efficiency
Optimized storage directly translates to increased overall efficiency. By preventing bottlenecks, the system allows for consistent resource flow. This improves productivity, minimizes downtime, and maximizes resource utilization. A well-designed storage system, with appropriate capacity and placement, effectively manages fluctuations and irregularities in the production pipeline, contributing to a stable and productive industrial operation.
In conclusion, strategic storage capacity is essential for preventing pipeline overextension. By creating a buffer between different stages of production, storage facilities effectively manage fluctuating throughput and mitigate bottlenecks. This mitigation allows the production system to function at its maximum efficiency, allowing players to effectively use resources, balance production, and ultimately, produce more in Factorio. The optimal storage system acts as a vital element in optimizing the entire factory layout and minimizing disruption to the pipeline.
7. Logistics Design
Effective logistics design is fundamental to preventing pipeline overextension in Factorio. A poorly conceived or implemented logistical system directly contributes to bottlenecks and inefficiencies within the production pipeline. The flow of resources, from raw materials to finished products, relies heavily on the efficiency of transportation routes, storage facilities, and overall resource allocation. A poorly designed system, characterized by congestion and delays, leads to an overextended pipeline, reducing output and impacting the entire factory's productivity. Consider a factory with a high throughput of copper ore. Without a well-defined logistics system, the surplus of raw material will accumulate, overwhelming subsequent processing stages and causing an overextended pipeline. This principle applies to virtually every aspect of Factorio production, highlighting the critical importance of proper logistics design.
A well-designed logistics system in Factorio anticipates the volume and velocity of resource movement. This includes careful planning of conveyor belt layouts, train tracks, and storage locations. Redundancy in transport paths is a vital element. Diversification of transport routes minimizes vulnerability to disruptions, ensuring that if one route experiences congestion, alternative pathways can accommodate the flow. This redundancy is analogous to the concept of alternate roads in real-world transportation networks, allowing for continued operation despite temporary blockages or increased traffic. Furthermore, optimized storage locations are crucial for preventing backlogs. Strategically placed storage facilities between production and processing stages act as buffers, smoothing out variations in production and processing speeds, and ensuring uninterrupted throughput. In essence, the logistics design acts as the framework that dictates the flow of goods, directly affecting the production pipeline's health.
Understanding the connection between logistics design and pipeline overextension is vital for optimizing Factorio factories. A well-defined logistical infrastructure prevents congestion, minimizes bottlenecks, and maximizes the throughput of resources. This in turn enhances overall efficiency and productivity. Properly designed logistics systems are not merely a component but a crucial driver of a smoothly functioning Factorio factory. Implementing sound logistics strategies allows players to effectively manage their resources, balance production, and achieve optimal output in the game, directly relating to minimizing the risk of pipeline overextension. By understanding the importance of logistics, players can design more efficient and resilient industrial systems.
Frequently Asked Questions
This section addresses common concerns and misconceptions regarding pipeline overextension in Factorio. Understanding these issues is crucial for optimizing resource flow and maximizing production efficiency.
Question 1: What is pipeline overextension in Factorio?
Pipeline overextension occurs when the rate at which resources are produced or processed exceeds the capacity of the transportation or processing system. This results in a buildup of resources at various points in the production chain, creating bottlenecks and hindering overall efficiency. The system becomes congested, and production slows down or stops completely.
Question 2: What are the primary causes of pipeline overextension?
Several factors contribute to pipeline overextension. Imbalances in production rates between different stages of the production chain, insufficient conveyor or train capacity, slow processing speeds, inadequate storage, and poorly planned logistics designs are common culprits. Each component must be considered in conjunction with others.
Question 3: How can I identify pipeline overextension in my Factorio base?
Identifying pipeline overextension involves monitoring resource flow. Observe where items are piling up in the production chain. Look for bottlenecks in conveyor belts, train stations, or processing facilities. Examine the storage capacity of intermediate stations; insufficient storage often exacerbates the problem. Pay close attention to output queues at each stage to detect delays and potential bottlenecks.
Question 4: What are some solutions to prevent or mitigate pipeline overextension?
Mitigation strategies include increasing the capacity of conveyor belts, trains, or processing facilities. Employing intermediate storage, carefully planning logistics, ensuring balance in production rates across all stages, and upgrading automated production systems are crucial. Address the bottleneck directly by improving the slowest link in the chain.
Question 5: What is the impact of pipeline overextension on Factorio game play?
Pipeline overextension significantly reduces overall production efficiency. It leads to wasted resources, prolonged delays, and a decrease in the rate at which desired products are produced. The result is a less efficient, less profitable, and sometimes frustrating experience for the player.
Understanding these issues will greatly assist in streamlining production lines and optimizing resource flow in Factorio, ultimately leading to more efficient and rewarding gameplay.
Moving forward, this document will delve into specific strategies for designing efficient production chains in Factorio.
Conclusion
This exploration of pipeline overextension in Factorio underscores the critical importance of a balanced and optimized production system. Inadequate conveyor capacity, mismatched processing speeds, imbalanced production rates, insufficient storage, and flawed logistics design are all major contributors to this critical bottleneck. Understanding the interplay of these factors is essential for efficient resource management. Resource imbalances, whether due to unexpected demand fluctuations or poorly planned production rates, directly translate into reduced output and wasted resources. Properly addressing these imbalances is not simply about maximizing throughput, but about ensuring the sustainable operation of the entire industrial network.
Successfully navigating the complexities of Factorio's industrial systems requires a proactive approach to production planning. Proactive monitoring of resource flow, capacity limitations, and strategic placement of storage facilities are crucial for preventing and mitigating pipeline overextension. This proactive approach not only optimizes resource usage but also allows for flexibility in responding to evolving production needs. Ultimately, a deep understanding of the interconnectedness of all these elements is key to achieving maximal efficiency and output within the Factorio game environment. Ignoring these aspects will inevitably lead to significant inefficiencies and a less satisfying experience for any player.
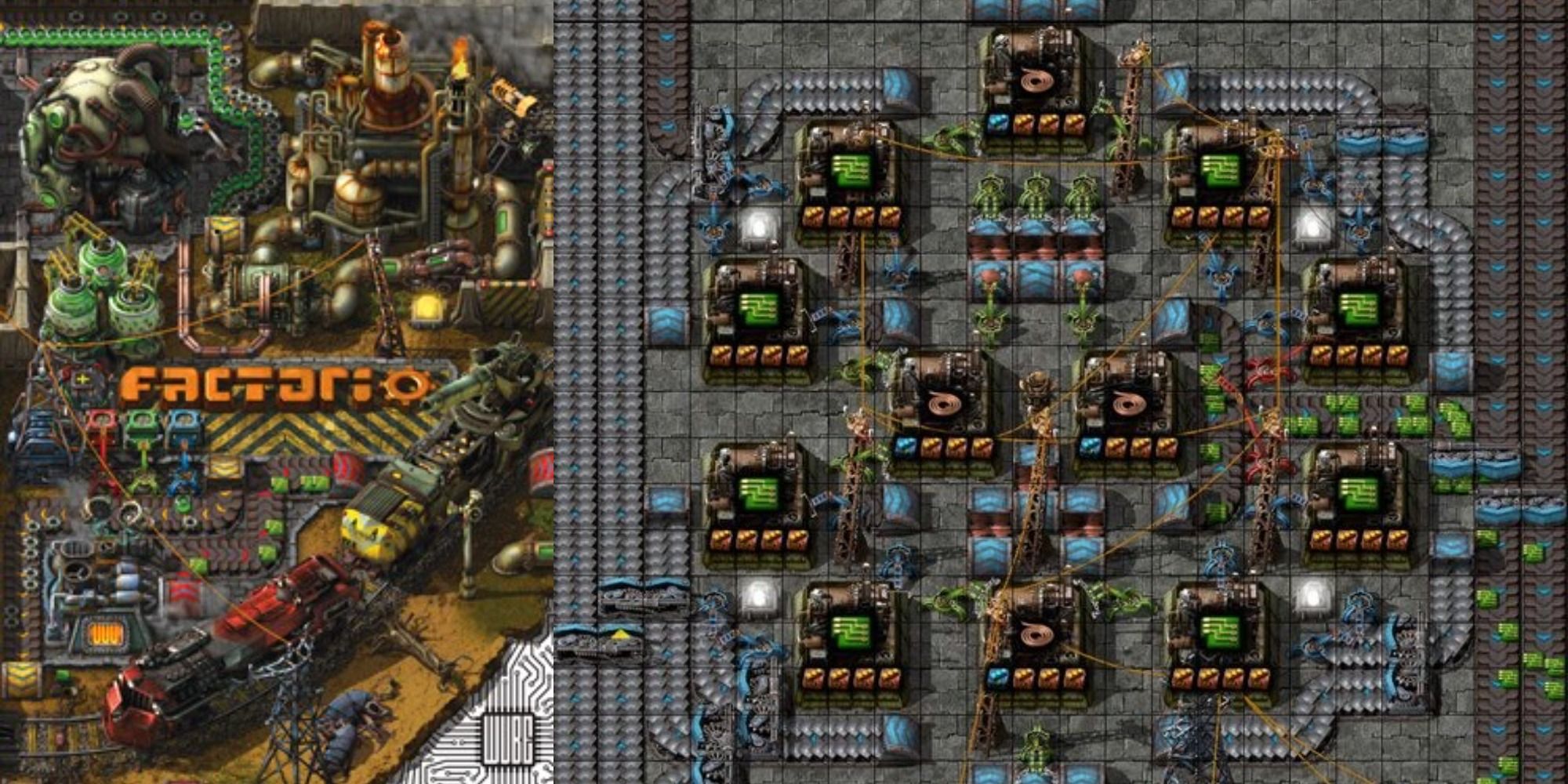

