Optimizing Production Chains: Strategies for Enhanced Efficiency in Factorio
Extended production chains in Factorio, often involving multiple interconnected belts and automated machinery, represent a crucial aspect of optimizing resource flow and maximizing output. These systems, carefully designed and managed, can dramatically affect the overall efficiency of a base. They go beyond basic setup and require meticulous planning to ensure smooth, uninterrupted throughput.
Efficiently routing resources through linked production stagesfrom raw materials to finished goodsis central to successful Factorio gameplay. This often involves strategically placing automated assemblers, conveyors, and storage facilities in sequences to process items with minimum downtime and maximum speed. Considerations such as belt width, processing times, and intermediate storage needs are critical to maintaining a consistent production cadence. Optimizing such a system requires a profound understanding of the game's mechanics and an iterative approach to improvement. Balancing the demands of individual crafting stations with the overall throughput capacity of the system is fundamental.
The importance of a well-structured production system lies in its ability to maximize resource utilization and speed. Minimizing bottlenecks and delays through strategic placement and careful planning directly impacts the rate at which resources can be turned into usable products. This is vital in both early-game resource gathering and later-game advanced production cycles. Successful setup, often involving multiple levels of refinement, dramatically increases the rate of output, crucial for large-scale manufacturing. The ability to sustain production and meet increasing demands is directly correlated with an effectively designed, extended crafting system.
Moving forward, exploring various techniques for optimizing extended crafting systems will be covered. This includes analyzing different assembly line architectures, optimizing resource management, and assessing methods for handling fluctuating demands. Crucially, we will discuss the importance of automation in large-scale production and the roles of different automated mechanisms within a system.
Factorio Pipeline Over Extended
Optimizing resource flow in Factorio's complex production systems hinges on effectively managing extended pipelines. Strategic design and implementation are essential for maximizing output and minimizing bottlenecks.
- Resource flow
- Automated systems
- Throughput optimization
- Bottleneck mitigation
- Inventory management
- Modular design
- Scalability
Efficient resource flow through a network of automated systems is crucial. Throughput optimization involves minimizing delays at each stage. Addressing bottlenecks prevents production slowdowns. Proper inventory management ensures consistent supply to downstream processes, while a modular design allows adaptation to changing needs. Such a system must inherently be scalable to handle increasing demands. Real-world examples, from assembly lines to complex supply chains, illustrate the principle of optimizing extended production systems for peak performance, ensuring each component contributes to the overall outcome.
1. Resource flow
Effective resource flow is fundamental to the success of an extended Factorio pipeline. The pipeline's efficiency hinges on the seamless movement of resources from initial acquisition to final product. A well-orchestrated flow minimizes bottlenecks and maximizes throughput. Interruptions or delays in any stage of resource transport directly affect the entire pipeline, impacting the output rate and overall production. Imagine a manufacturing assembly line: a blockage at one point halts the entire process. Similar principles apply in a Factorio production chain; impediments in resource flow translate to reduced productivity.
The direct link between resource flow and the extended pipeline's efficiency is evident in practical application. Adequate storage capacity is critical, acting as a buffer between production stages. This buffer mitigates the impact of temporary fluctuations in supply or demand. Optimal placement of conveyors, belt widths carefully calibrated to the rate of production, and strategic placement of assemblers all directly affect resource flow. When these elements are meticulously considered and implemented, the entire extended pipeline operates at a higher capacity, supporting a robust and consistent supply chain for products. Consider real-world examples of logistics systems: optimized routes, efficient warehousing, and just-in-time inventory management principles all directly translate to effective resource flow.
Understanding the intricate relationship between resource flow and extended pipelines is essential for effective Factorio design. Problems in resource flow, such as insufficient storage, inadequate conveyor systems, or bottlenecks in the manufacturing process, ultimately restrict the pipeline's potential. To maximize output in extended Factorio pipelines, a meticulous understanding of resource flowits constraints, causes of delays, and optimal management strategiesis critical. This understanding translates to efficient resource allocation, minimized waste, and enhanced output. Ultimately, an efficient, extended pipeline relies on consistent and uninterrupted resource flow.
2. Automated Systems
Automated systems are integral to the efficacy of extended Factorio pipelines. Their role extends beyond simple task automation; they are a fundamental component enabling complex and sophisticated production chains. Automated machinery, from assemblers and conveyors to storage systems, enables the high-throughput capability of extended pipelines. Efficiency gains stem from the automated systems' ability to handle repetitive tasks with minimal human intervention and consistent speed.
The integration of automated systems directly influences a pipeline's capacity and flexibility. Automated conveyors, for instance, ensure continuous movement of resources between production stages, minimizing delays. Automated assemblers guarantee consistent product quality and output across numerous production runs. Robust storage solutions, managed automatically, prevent resource bottlenecks and maintain adequate inventory levels. This interplay of automated components creates a cohesive and responsive system, adapting to fluctuating demands and maintaining consistent production. Real-world examples of automated manufacturing processes highlight the impact of interconnected automated systems on throughput and output efficiency. Modern car assembly lines, for instance, showcase how automated systems enable sustained production of complex products at high rates.
Successfully managing extended Factorio pipelines hinges on the effective implementation and management of automated systems. Understanding the intricacies of automation is paramount to optimizing resource flow and production output. Furthermore, maintaining and troubleshooting automated systems requires specialized knowledge. An effective understanding of automated systems, particularly within the context of extended Factorio pipelines, minimizes production downtime and maximizes output capacity. This knowledge base is vital for optimizing throughput, mitigating bottlenecks, and responding effectively to production challenges in complex, dynamic environments.
3. Throughput optimization
Maximizing throughput in extended Factorio pipelines is paramount to efficient resource management and production. Throughput optimization, in this context, involves strategically minimizing delays and bottlenecks along the entire production chain to achieve the highest possible output rate. It necessitates a thorough understanding of resource flows, processing times, and the interplay of various production components.
- Minimizing Bottlenecks
Identifying and mitigating bottlenecks is crucial. A bottleneck, anywhere in the production pipeline, can significantly reduce the overall throughput. This could involve optimizing resource allocation at specific crafting stations, ensuring adequate storage capacity, or adjusting conveyor belt widths to match the rate of processing. Analyzing production times and comparing them to transport speeds helps pinpoint potential congestion points. For example, an assembly station operating slower than the input conveyor could become a bottleneck. Addressing this bottleneck by increasing the assembler's speed, adjusting the input conveyor speed or both, directly increases throughput.
- Inventory Management
Efficient inventory management directly correlates to enhanced throughput. Balancing the need for raw materials with the output rate of finished goods is key. This necessitates optimizing storage capacity to avoid shortages or surpluses. Excess inventory occupies valuable space, while shortages disrupt production flows. Examples from real-world manufacturing illustrate this: just-in-time inventory systems maintain optimal stock levels for high throughput. Effective inventory management in extended Factorio pipelines ensures timely availability of materials while preventing unnecessary storage demands.
- Modular Design and Flexibility
The design of the extended Factorio pipeline should allow for modular adjustments. The ability to add or remove production components without disrupting the entire system is critical for adaptability. This flexibility, allowing for adjustments in response to fluctuations in demand or changes in product types, directly influences throughput optimization. Modular designs enable dynamic responses to evolving production needs. Imagine an assembly line designed to produce various product types; modular sections allow easy switching between production lines without extensive reconfiguration.
- Streamlined Resource Flow
Streamlining resource flow through the pipeline minimizes interruptions. Optimizing conveyor layouts, considering the number and size of belts, as well as adjusting the allocation of resources for different product types are crucial. Careful consideration of processing time at each stage, including crafting, transporting, and storing, is paramount. This involves understanding how individual production steps influence the overall flow. Efficiently routing resources through the pipeline, ensuring there are no dead ends or points of congestion, will maximize throughput by maintaining a consistent, predictable flow.
In conclusion, optimizing throughput in extended Factorio pipelines necessitates a comprehensive approach. Addressing bottlenecks, managing inventory, designing for flexibility, and streamlining resource flow are critical aspects. By prioritizing these elements, Factorio players can build production systems that effectively transform raw materials into finished products at the fastest possible rate, a key aspect of successful gameplay. Such knowledge effectively translates to effective management of resources and high-output production, central to success in Factorio.
4. Bottleneck Mitigation
Bottleneck mitigation is a critical component of successful extended Factorio pipelines. A bottleneck, anywhere within the resource flow or production process, significantly reduces the overall throughput of the system. This reduction in throughput translates directly to decreased output and efficiency. A poorly designed or inadequately managed pipeline, lacking appropriate mitigation strategies, suffers from diminishing returns, slowing production far beyond the rate of individual component efficiency. The interconnected nature of Factorio pipelines necessitates a holistic approach to ensure that inefficiencies at any point don't cripple the entire system.
Identifying bottlenecks is the first step in mitigation. This involves careful analysis of resource flows, production rates, and processing times at each stage. For example, an assembler operating slower than the input conveyor is a clear bottleneck. Excess inventory or insufficient storage capacity can also create bottlenecks, causing production delays. In complex extended pipelines, a slowdown in one aspect of production can cascade throughout the entire system, creating a ripple effect of inefficiencies. Real-world manufacturing systems provide analogous examples: if a part is difficult to access on an assembly line, the entire line can become stalled. Recognizing these potential chokepoints is crucial for implementing effective mitigation strategies. This strategic identification of bottlenecks is a critical element of effective production design in Factorio.
Mitigation strategies encompass various approaches, including adjustments to resource allocation, optimization of conveyor systems, and enhancements to production facilities. Streamlining resource flow through the pipeline, ensuring that each component operates at its optimal capacity, and appropriately balancing demand with production capacity are crucial. Efficient inventory management plays a key role in avoiding potential inventory shortages or surpluses that can cause bottlenecks. The understanding of interconnected components and their influence on overall throughput is essential. Efficiently managing resource flow, optimizing storage, and carefully adjusting production rates are central to effective bottleneck mitigation, enabling smooth operation of extended Factorio pipelines. Ultimately, the goal is to create a harmonious flow of resources, preventing points of congestion and maximizing output throughout the pipeline.
5. Inventory Management
Effective inventory management is intrinsically linked to the success of extended Factorio pipelines. A well-managed inventory acts as a vital buffer within the system, ensuring a steady flow of resources to downstream production stages. Adequate stock levels prevent bottlenecks, maintain consistent production rates, and avoid production halts due to material shortages. Conversely, poor inventory management can lead to significant delays and disruptions in the pipeline, diminishing overall efficiency. The delicate balance between procuring sufficient resources and avoiding excessive stockpiling is critical.
In extended Factorio pipelines, the interconnected nature of production stages amplifies the impact of inventory fluctuations. If one stage experiences a temporary shortage of materials, it can ripple through the entire pipeline, causing cascading delays and ultimately reducing overall output. This principle mirrors real-world manufacturing processes, where disruptions in the supply chain can halt entire production lines. Consequently, a robust inventory management strategy is essential to mitigate these risks. This includes accurately forecasting material demands, establishing appropriate storage capacity, and implementing automated systems for tracking and replenishing inventory. Efficient inventory management is critical for consistent throughput. A properly managed inventory buffer will minimize the effects of temporary imbalances in supply and demand.
The significance of inventory management in extended Factorio pipelines extends beyond simply avoiding production halts. It also directly affects the scalability of the production system. A well-structured inventory system allows for more efficient resource allocation and can facilitate an increase in production output without proportionately increasing the complexity of the system's design. This adaptability is particularly valuable in dynamically changing conditions or during periods of escalated production. By maintaining an optimized inventory, the extended pipeline becomes more resilient and adaptable to variations in material availability and production demands. Efficient inventory management, therefore, is not just a good practice but a vital component for successfully scaling and adapting extended Factorio production systems.
6. Modular Design
Modular design in extended Factorio pipelines is crucial for adaptability and scalability. A modular approach allows for flexible adjustment and expansion of production systems without requiring complete redesign. This adaptability is vital for accommodating changes in resource availability, product demands, and technological advancements. It promotes efficiency by facilitating the addition or removal of components without disrupting the overall flow.
- Adaptability to Changing Demands
Modular design enables swift adjustments to production needs. If resource availability changes, or demand for a particular product increases or decreases, modular components can be added or removed without extensive reconfiguration. This adaptability is critical in dynamic environments where production requirements are not static. Modifications become easier, as the impact of adjustments is localized, minimizing disruptions to the entire system.
- Scalability and Expansion
Modular design enables the incremental expansion of production capacity. Additional modules can be added to increase the throughput of the pipeline without replacing existing components. This is particularly advantageous in Factorio, where production demands can increase significantly over the course of gameplay. Scalability is a direct consequence of modular design, enabling production systems to keep pace with increasing resource needs. This approach avoids the need for complete overhaul of the production chain.
- Simplified Maintenance and Troubleshooting
Modular design simplifies maintenance and troubleshooting. If a specific module malfunctions, it can be isolated and repaired without disrupting the entire pipeline. This localized approach to maintenance minimizes downtime, and reduces the risk of cascading failures in a complex system. The modularity in design directly enhances the ease of diagnosis and repair, improving the reliability of the production chain. This also facilitates easier upgrades and the incorporation of improved technologies.
- Reduced Risk of Cascading Failures
Modular components are often designed to be relatively independent. A malfunction in one module is less likely to trigger a failure in adjacent modules. This minimized risk of cascading failures is a significant advantage, especially in complex, interconnected systems. The independence afforded by modular design helps ensure that problems remain confined to their source, safeguarding against widespread disruption within the entire production pipeline.
In summary, a modular approach to design allows for responsive adjustments to production requirements, facilitating efficient scaling, streamlined maintenance, and reduced vulnerability to cascading failures. These advantages translate directly to the sustained productivity of an extended Factorio pipeline. This adaptability is critical in dynamic environments where efficient production must remain consistent amidst changing circumstances.
7. Scalability
Scalability in the context of extended Factorio pipelines is the capacity of a production system to adapt to increasing demands and resource needs without fundamental redesign. A scalable pipeline seamlessly accommodates growth in production throughput, maintaining efficiency as output levels rise. This critical characteristic is essential for sustained progress and success in Factorio, where production challenges often evolve from simple resource gathering to complex, large-scale manufacturing.
- Adaptability to Expanding Resource Needs
A scalable pipeline can handle increasing demands for raw materials. As production increases, the pipeline adapts by efficiently routing more resources from gathering points to processing stages, without creating bottlenecks or bottlenecks. This adaptability often requires careful consideration of storage capacity, conveyor belt widths, and the speed of processing units. Maintaining a balance between throughput and storage capacity is a critical aspect of a scalable design. Expanding resource allocation to more complex and resource-intensive items is facilitated by effective scaling.
- Handling Increased Product Output
A scalable pipeline must adjust to rising demand for finished goods. This means the pipeline can handle a surge in output without significant disruptions in efficiency. This might involve adding processing units, augmenting storage facilities, or adjusting conveyor systems to accommodate increased throughput. A good example of scaling includes adding more assemblers to the line to increase finished goods production if the output rate from previous stages matches. Effective scaling anticipates future demands and ensures sustained production capacity.
- Efficient Resource Allocation and Management
A scalable pipeline efficiently manages resource allocation as the system expands. This requires careful planning for new resources and the integration of new production stages without disrupting existing operations. As the scale increases, the network of conveyors and storage units needs to be appropriately adjusted to maintain a smooth flow of resources. Efficient allocation is critical for keeping pace with production targets without unnecessary waste. This includes optimizing resource collection strategies and storage methods to accommodate expanded needs.
- Maintaining Efficiency Amidst Expansion
Scalability in extended Factorio pipelines goes beyond mere expansion. It ensures that the increased production capacity comes with a maintenance of efficiency. Adding components must not cause bottlenecks or negatively impact existing processes. This requires a meticulous understanding of production times, resource allocation, and the interconnectedness of different components within the pipeline. A properly scaled system maximizes productivity per unit of resources, balancing production capacity with available materials. The system needs to maintain its effectiveness and consistency as production output expands.
In conclusion, scalability in Factorio's extended pipelines is not just about increasing output; it's about maintaining efficiency and adaptability. A well-designed and scalable pipeline can handle sustained growth in production, providing a competitive advantage in the long term. Strategic planning and adjustments to component placement, resource allocation, and throughput capacity ensure that production keeps pace with increasing needs without sacrificing overall efficiency. This resilience to evolving demands and growth is critical to sustaining production as the player's base expands and develops.
Frequently Asked Questions
This section addresses common questions and concerns regarding optimizing production pipelines in Factorio. Properly designed pipelines are essential for efficient resource management and maximum output.
Question 1: What are the key indicators of an inefficient Factorio pipeline?
Answer 1: Inefficient pipelines often exhibit bottlenecks, characterized by slowdowns or stalls in the flow of resources at specific points. Excessive inventory buildup upstream or shortages downstream are also indicators. Inconsistent production rates and significant discrepancies between intended output and actual output suggest pipeline inefficiencies. Analysis of conveyor speeds, processing times, and storage capacity can pinpoint areas needing improvement.
Question 2: How can I identify bottlenecks in a complex pipeline?
Answer 2: Analyze the flow of resources at each stage. Pay close attention to points where resources accumulate or where production rates drop sharply. Examine the processing time at each assembler, comparing it to the transit times between stations. This detailed examination will likely reveal bottlenecks and areas requiring adjustment, be it changes in conveyor speed, storage capacity, or production rates within individual units.
Question 3: What role does inventory management play in optimizing a Factorio pipeline?
Answer 3: Inventory management is critical for maintaining a steady flow of materials. Adequate storage capacity prevents shortages, while excessive inventory wastes resources. Striking a balance between having enough raw materials and avoiding excess stock is essential. Real-time monitoring of inventory levels and proactive adjustments to resource collection rates and production targets are essential.
Question 4: How can I ensure my Factorio pipeline scales effectively with increasing production needs?
Answer 4: Employ a modular design approach. This means the pipeline's components should be easily adaptable and expandable. Using modular components allows adjustments to throughput without complete system redesign. Properly anticipating future production increases through careful planning and component selection is paramount.
Question 5: What strategies exist for mitigating bottlenecks in an extended Factorio pipeline?
Answer 5: Implementing strategies such as optimizing conveyor layouts, carefully considering belt widths, and adjusting production speeds at individual stations can greatly improve throughput. Streamlining resource flow and maintaining adequate storage capacity are crucial. Strategic use of automated systems and meticulous monitoring of material flow can minimize the occurrence of bottlenecks and optimize overall throughput.
Understanding the principles of efficient resource flow and effective inventory management enables the construction of optimized Factorio pipelines. A thorough understanding of these considerations is essential for maximizing production efficiency and productivity within the Factorio environment.
The next section will explore specific strategies for implementing these optimization techniques in various production scenarios.
Conclusion
This exploration of optimizing Factorio pipelines, particularly those extended across multiple production stages, reveals a multifaceted approach to achieving peak efficiency. Key elements identified include strategic resource flow management, effective inventory control, and the crucial role of automated systems. Understanding and addressing bottlenecks, critical impediments to throughput, are paramount. Furthermore, a modular design fosters adaptability to evolving production needs and scales effectively with increasing resource demands. The interconnectedness of each pipeline component emphasizes the necessity for a holistic perspective in optimizing the entire system. Ignoring any single aspect can lead to performance degradation. Maximizing throughput, minimizing downtime, and ensuring a steady flow of resources from initial acquisition to final product are fundamental to the success of an extended Factorio pipeline.
Optimizing extended pipelines requires a thoughtful balance of design considerations. A comprehensive understanding of production rates, processing times, and resource requirements is essential for effective implementation. Continuous monitoring and iterative adjustments are crucial for maintaining peak performance in dynamic production environments. Further research and experimentation could explore the impact of specific technology choices on pipeline efficiency, potentially revealing optimal configurations for various production scenarios. The insights gained from analyzing extended pipelines offer valuable lessons transferable to various resource management and production systems, not just within the confines of Factorio. A meticulous understanding of these principles yields not only elevated output but also a more deeply nuanced grasp of optimizing complex systems in general.
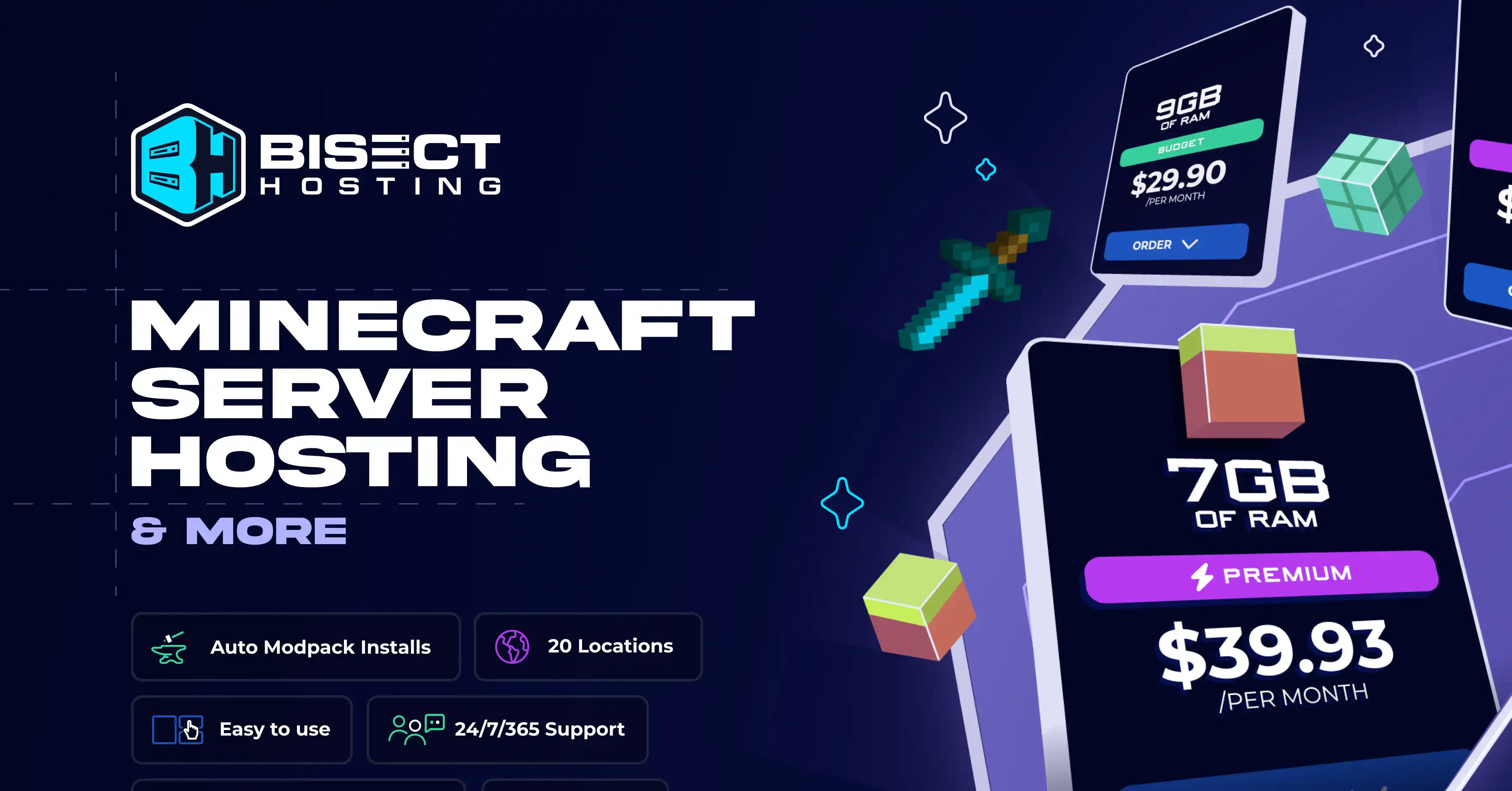
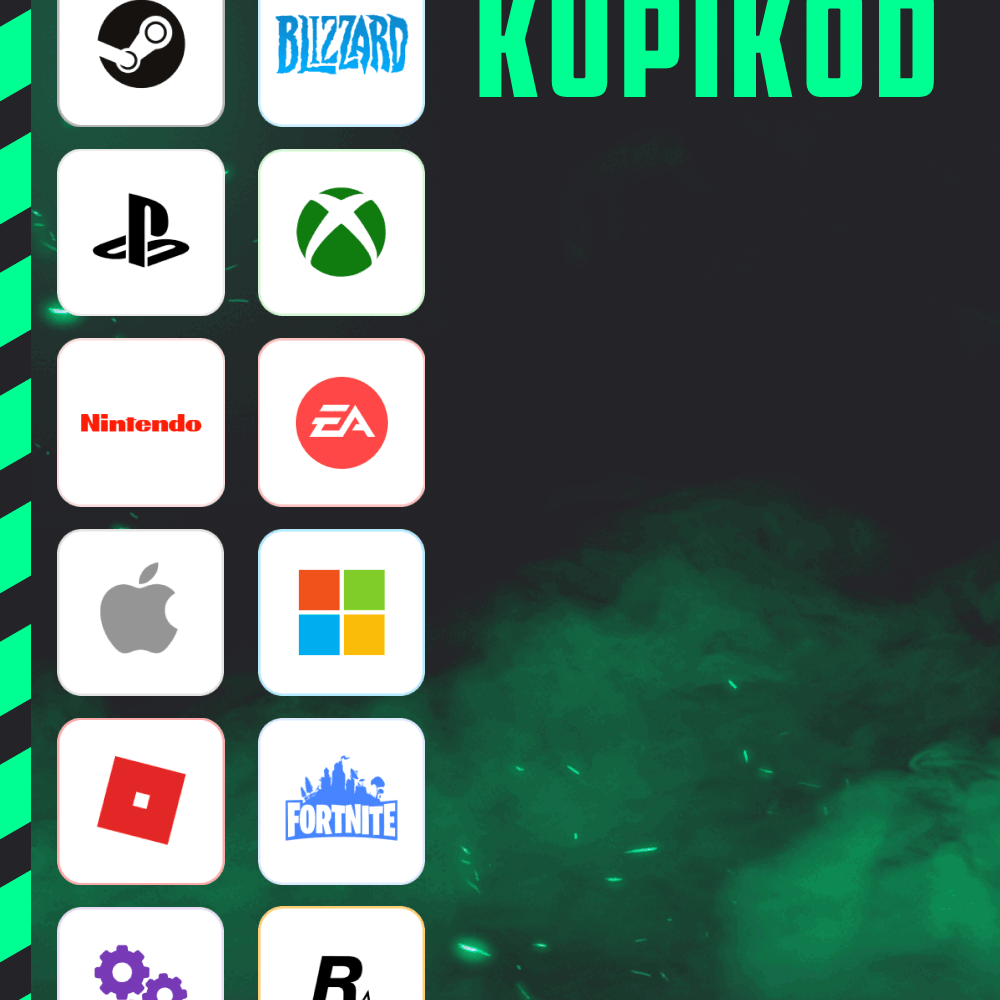
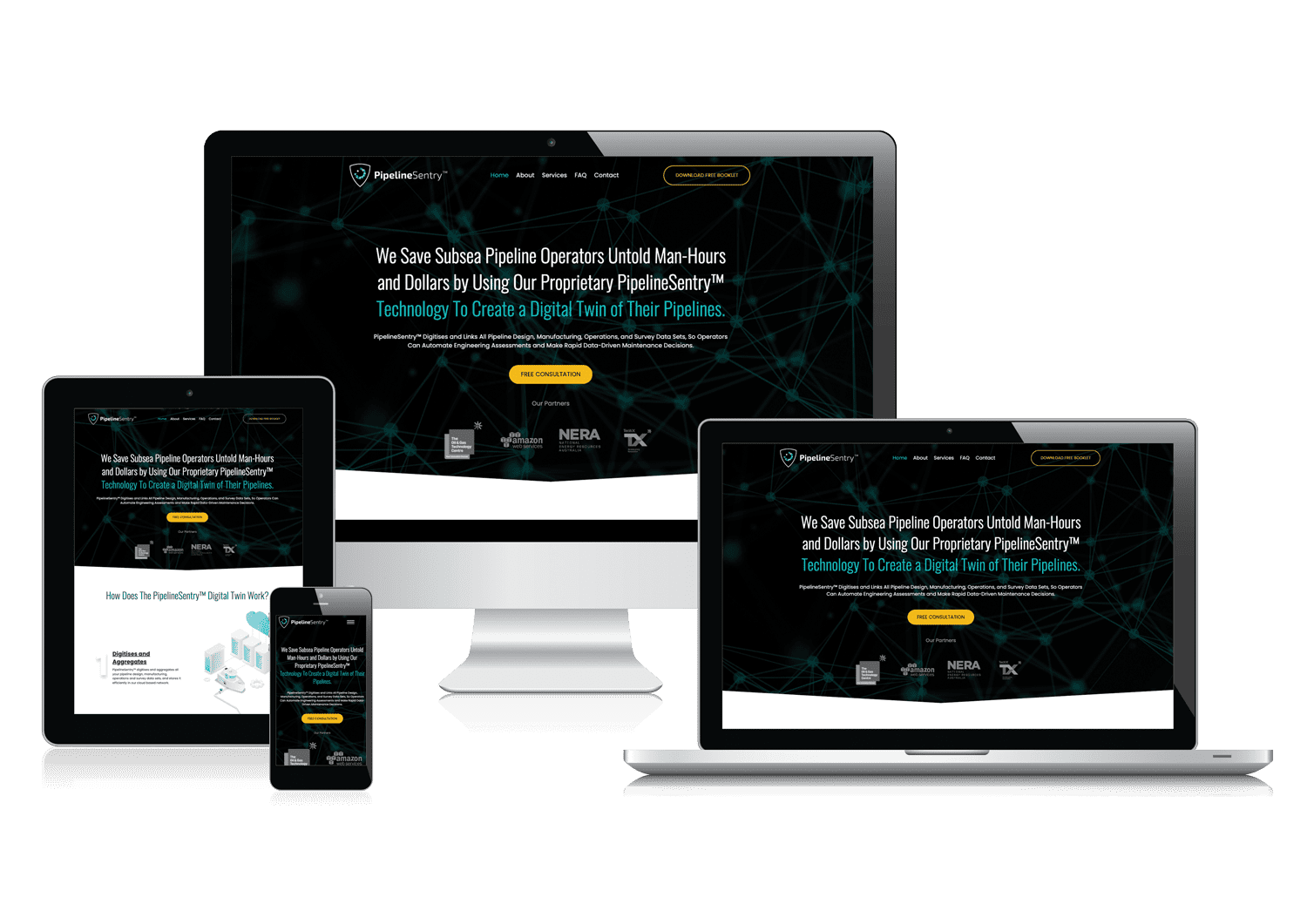